
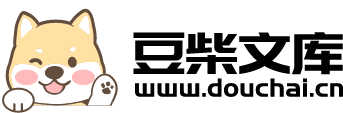
一种奥氏体不锈钢离子氮化催渗工艺.pdf
是来****文章
在线预览结束,喜欢就下载吧,查找使用更方便
相关资料
一种奥氏体不锈钢离子氮化催渗工艺.pdf
本发明涉及一种不锈钢离子氮化工艺,尤其涉及一种奥氏体不锈钢离子氮化催渗工艺,该工艺主要包括以下步骤:1)对不锈钢工件表面清洗,去除工件表面油污和杂质;2)对不锈钢工件进行预氧化处理;3)待不锈钢工件冷却后,将其放入离子氮化炉内,通入经过干燥后的氢气,然后起辉升温,待达到一定温度后,通入氮气,调节氮气和氢气比例、炉内压力随后开始计时,渗氮一定时间后,关闭离子氮化炉,工件随炉冷却。采用该工艺处理的奥氏体不锈钢可以获得比常规离子氮化工艺更厚的化合物层。
一种奥氏体不锈钢分段式加压固溶氮化催渗方法.pdf
一种奥氏体不锈钢分段式加压固溶氮化催渗方法,其主要是:将奥氏体不锈钢置于专利名称为“一种具有双压平衡结构的增压高温氮化装置”专利号为201210530358.6固溶氮化炉中,并以0.5-2L/min流速通入NH3至炉内压强到达0.1~1.0MPa范围,在温度为500~700℃下进行NH3氮化预处理5~10h;再将上述固溶氮化炉内NH3完全排出并以1-5L/min流速通入N2至炉内压强到达0.1~1.0MPa范围,后将炉温迅速升至900~1200℃,在此条件下进行N2固溶氮化处理1~20h,随后快速水冷至室
不锈钢催渗氮化新工艺的研究.docx
不锈钢催渗氮化新工艺的研究不锈钢催渗氮化新工艺的研究摘要:随着工业的发展,对材料表面性能的要求也越来越高。不锈钢是一种常用的金属材料,在多种领域都有广泛应用。然而,不锈钢的表面硬度和耐磨性相对较低,限制了其进一步应用的范围。因此,本文研究了一种催渗氮化的新工艺,以提高不锈钢材料的表面硬度和耐磨性,并通过实验验证了该工艺的可行性。关键词:不锈钢;催渗氮化;表面硬度;耐磨性1.引言不锈钢是一种含铬量高达10.5%以上的合金钢,具有良好的耐腐蚀性和抗氧化性。然而,由于不锈钢的普通组织结构和成分,其表面硬度相对较
一种奥氏体不锈钢渗铬氮化表面处理工艺.pdf
本发明属于核燃料制造领域,具体涉及一种奥氏体不锈钢渗铬氮化表面处理工艺,将工件埋入渗铬剂,再一同装入渗铬罐再入渗铬炉进行渗铬热处理,将工件置于高压真空气淬炉,渗铬层转化为渗铬氮化复合渗层,渗铬剂其成分为铬粉、填充剂和催化剂,渗铬热处理首先进行渗铬粉剂预处理及装载封装,再进行热处理;氮化处理包括清洗并干燥试样、工件和氮化炉,之后氮化炉进行渗氮热处理。渗铬剂配方避免了板结现象,对工造不易造成损伤,设计渗铬保温时间因素与渗层厚度之间的关系,控制渗铬层厚度,以及减小工件变形,固溶氮化工艺能够满足氮化要求,且消除了
奥氏体不锈钢低温离子渗氮工艺研究.docx
奥氏体不锈钢低温离子渗氮工艺研究标题:奥氏体不锈钢低温离子渗氮工艺研究摘要:本文以奥氏体不锈钢材料为研究对象,探讨了低温离子渗氮工艺对不锈钢材料性能的影响。通过采用扫描电子显微镜(SEM)、X射线衍射(XRD)和硬度测试等表征手段对材料的显微结构、相组成以及硬度进行了分析。结果表明,采用低温离子渗氮工艺处理的不锈钢材料具有更优异的性能,其硬度得到了显著提升,同时硬化层析分布均匀、致密,能够有效提高材料的抗磨损和抗腐蚀性能。关键词:奥氏体不锈钢;低温离子渗氮;显微结构;相组成;硬度1.引言奥氏体不锈钢具有优