
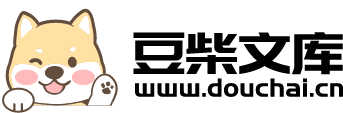
一种奥氏体不锈钢渗铬氮化表面处理工艺.pdf
是笛****加盟
在线预览结束,喜欢就下载吧,查找使用更方便
相关资料
一种奥氏体不锈钢渗铬氮化表面处理工艺.pdf
本发明属于核燃料制造领域,具体涉及一种奥氏体不锈钢渗铬氮化表面处理工艺,将工件埋入渗铬剂,再一同装入渗铬罐再入渗铬炉进行渗铬热处理,将工件置于高压真空气淬炉,渗铬层转化为渗铬氮化复合渗层,渗铬剂其成分为铬粉、填充剂和催化剂,渗铬热处理首先进行渗铬粉剂预处理及装载封装,再进行热处理;氮化处理包括清洗并干燥试样、工件和氮化炉,之后氮化炉进行渗氮热处理。渗铬剂配方避免了板结现象,对工造不易造成损伤,设计渗铬保温时间因素与渗层厚度之间的关系,控制渗铬层厚度,以及减小工件变形,固溶氮化工艺能够满足氮化要求,且消除了
一种奥氏体不锈钢工件渗铬氮化用电阻炉及渗铬氮化方法.pdf
本发明公开了一种奥氏体不锈钢工件渗铬氮化用电阻炉及渗铬氮化方法,该渗铬氮化用电阻炉包括炉体和真空室;该方法包括渗铬方法和氮化方法,渗铬方法包括步骤一、真空室的吊装;步骤二、真空室内工件及渗铬粉的设置;步骤三、真空室的封闭;步骤四、传感器的安装;步骤五、真空室内部抽真空;步骤六、工件的加热;步骤七、工件的冷却;氮化方法包括步骤S1、准备工作;步骤S2、真空室内工件的吊装;步骤S3、真空室的封闭;步骤S4、真空室内部气体的置换;步骤S5、复步骤S4四次~八次;步骤S6、工件的加热;步骤S7、工件的冷却。本发明
一种奥氏体不锈钢离子氮化催渗工艺.pdf
本发明涉及一种不锈钢离子氮化工艺,尤其涉及一种奥氏体不锈钢离子氮化催渗工艺,该工艺主要包括以下步骤:1)对不锈钢工件表面清洗,去除工件表面油污和杂质;2)对不锈钢工件进行预氧化处理;3)待不锈钢工件冷却后,将其放入离子氮化炉内,通入经过干燥后的氢气,然后起辉升温,待达到一定温度后,通入氮气,调节氮气和氢气比例、炉内压力随后开始计时,渗氮一定时间后,关闭离子氮化炉,工件随炉冷却。采用该工艺处理的奥氏体不锈钢可以获得比常规离子氮化工艺更厚的化合物层。
一种奥氏体不锈钢复合表面处理工艺.pdf
本发明属于金属表面改性技术领域,具体涉及一种奥氏体不锈钢复合表面处理工艺。该方法主要包括以下步骤:1)对工件表面清洗,去除工件表面油污和杂质;2)待不锈钢工件冷却后,将其放入离子氮化炉内,通入经过干燥后的氢气,然后起辉升温,待达到一定温度后,通入氮气,调节氮气和氢气比例、炉内压力随后开始计时;3)渗氮一定时间后,关闭氮气,通入经过干燥后的空气,并保温一定时间。采用该工艺处理后的不锈钢不仅提高了表面耐磨性,而且保持住了不锈钢自身优良的耐腐蚀性能。
一种基于表面塑性变形预处理渗铬工艺.pdf
本发明公开了一种基于表面塑性变形预处理渗铬工艺,金属零件表面塑性变形处理:在压力为3-4大气压下,将金属零件表面喷砂4-6min,喷砂的砂子粒径在5-10μm;超声波清洗;浆料涂覆;烘干装炉;渗铬、炉冷。渗铬剂的各组分质量百分比为:Cr