
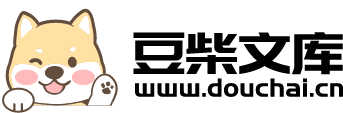
铁酸镁纳米颗粒的制备方法.pdf
贤惠****66
在线预览结束,喜欢就下载吧,查找使用更方便
相关资料
铁酸镁纳米颗粒的制备方法.pdf
一种铁酸镁纳米颗粒的制备方法,其特征在于:将镁粉与去离子水以1g:25mL~1g:30mL的比例混合所得的第一混合物在常温常压下超声水解得白色乳状胶体;将白色乳状胶体恒温烘干后研磨得Mg(OH)2纳米颗粒;按元素含量比Mg/Fe=1:2称取Mg(OH)2纳米颗粒与FeCl3·6H2O;将称取的Mg(OH)2纳米颗粒加入具有去离子水的第一烧杯中超声预处理1h;将称取的FeCl3·6H2O置入第二烧杯中,通过化学共沉淀法得Fe(OH)3沉淀,用去离子水将Fe(OH)3沉淀稀释为中性;将预处理的Mg(OH)2与
一种纳米铁酸镁的制备方法.pdf
一种纳米铁酸镁的制备方法,将FeCl3·6H2O与FeCl2·4H2O按摩尔比1∶1混合,滴加2mol/L的NaOH溶液,通过化学共沉淀法制备出磁性Fe3O4纳米粒子;再将其放入马弗炉500℃焙烧3-4h,得到纳米Fe2O3;将镁粉置于烧杯,加入去离子水,置于超声波清洗器处理5-8h,得到白色浑浊液;取上层浑浊液置干净烧杯中,入干燥箱恒温干燥,将所得产物研磨得纳米Mg(OH)2;将纳米Mg(OH)2放入马弗炉350℃下焙烧3-4h,将Fe3O4纳米粒子放入马弗炉500℃下焙烧3-4h;分别得到纳米MgO和
一种Au负载铁酸镧纳米颗粒的制备方法.pdf
本发明提供一种Au负载铁酸镧纳米颗粒的制备方法,其特征在于,包括步骤:将铁盐、硝酸镧溶于乙酸和乙二醇甲醚混合溶液,加入柠檬酸,滴加1wt%氯金酸溶液,60~80℃超声波环境下搅拌直到变为凝胶,静置陈化12小时后放入150~180℃烘箱中烘干,烘干后的粉体放入700~800℃马弗炉中焙烧3~6小时得到Au负载铁酸镧纳米颗粒粉体。本发明原料廉价,工艺简单,溶胶凝胶法一步合成Au负载铁酸镧纳米颗粒,合成材料的形貌控制稳定,所得产物Au和铁酸镧协同作用,可用于苯系物气体高效催化燃烧。
纳米矾酸铁的制备方法.pdf
一种纳米矾酸铁的制备方法,属于材料制备领域,其特征在于:将六水合三氯化铁溶于去离子水中,在磁力搅拌下加入等摩尔偏钒酸铵;搅拌片刻后将反应液转移至内衬聚四氟乙烯高温高压反应釜,经水热反应,生成黄色沉淀;然后将得到的沉淀过滤,用去离子水和无水乙醇各洗涤滤渣若干次,直至滤液无色;将滤渣置于真空烘箱烘干,得到钒酸铁前驱体;将前驱体置于马弗炉中高温煅烧,自然冷却后取出,用研钵研磨,得到矾酸铁制备完成。经过过滤、洗涤、干燥得到矾酸铁前驱体,再经过高温煅烧得到矾酸铁粉体,产物结晶性好、纯度高、粒径分布窄、分散性好。
铁酸铋纳米纤维的制备方法.pdf
本发明公开了一种铁酸铋纳米纤维的制备方法,用于解决现有的光催化材料带隙宽的技术问题。技术方案是将柠檬酸溶解到去离子水中形成柠檬酸溶液;再将硝酸铁、硝酸铋添加到柠檬酸溶液中搅拌至澄清透明,溶液静置放置后放在水浴锅中加热搅拌,向溶液中添加聚乙烯吡咯烷酮,继续搅拌至聚乙烯吡咯烷酮完全溶解,保持聚乙烯吡咯烷酮的浓度,利用注射泵和高压电源进行静电纺丝,用单晶硅片收集纤维;将收集到的纤维置于干燥箱中干燥后放入马弗炉中保温煅烧,得到铁酸铋纳米纤维,这种制备方法所制备的铁酸铋纳米纤维带隙宽度由背景技术的3.2~3.4ev