
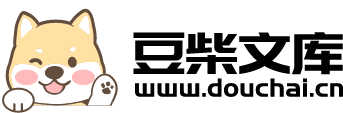
一种利用纳米复合电沉积技术对取向硅钢渗氮的方法.pdf
努力****南绿
在线预览结束,喜欢就下载吧,查找使用更方便
相关资料
一种利用纳米复合电沉积技术对取向硅钢渗氮的方法.pdf
本发明涉及一种利用纳米复合电沉积技术对取向硅钢渗氮的方法,包括以下步骤:1)按镀液组成称取各组分,滴加盐酸,调整pH值至2.5-3.1;2)将步骤1)中镀液超声分散30分钟,再使用电动搅拌器搅拌,将镀液水浴加热到40℃;3)将硅钢板清洗干净,选择10-30A/dm2的电流密度立即放入经过步骤2)的镀液中电镀,3-5分钟后取出,用蒸馏水洗净后自然晾干;以及4)将经过步骤3)的硅钢板放入气体保护炉中,进行热处理,保温时间为2小时。本发明的有益效果为:采用复合电沉积的技术,同时结合纳米技术与热处理的方法,在较低
一种基于渗氮装置的取向硅钢渗氮方法.pdf
本发明公开了一种基于渗氮装置的取向硅钢渗氮方法,属于冶金技术领域,尤其是取向硅钢生产装置、加工方法技术领域,解决现有设备不方便对停留在设备中的带钢长度进行调节,渗氮的效果需要通过控制带钢拉动的速度来进行调整,不容易控制,包括机架,所述机架顶部设置有机壳,所述机壳为横向设置的圆筒形结构,所述机壳的圆周面两侧均设置有连通其内部的矩形罩,且两个矩形罩内均设置有导电辊组,所述导电辊组包括平行设置在矩形罩内的两个导电密封辊,两个导电密封辊的两端均与矩形罩的内壁形成转动连接。本发明可以调整停留在机壳下部空间内的带钢长
一种取向硅钢的感应加热渗氮方法.pdf
一种取向硅钢的感应加热渗氮方法:经过冶炼、连铸后对铸坯加热并热轧、常化、冷轧及脱碳工序;在感应渗氮炉内进行两段渗氮处理:在干式N2气氛下自然冷却至室温,涂隔离剂、高温净化退火后待用。本发明的渗氮方法得到的氮化物多且分布均匀,渗层深度可到钢板厚度中心部位,钢板厚度中心部位AlN颗粒在每平方微米上达到1~1.5个,最终获得磁性能稳定,偏差小即批次之间波动不超过0.02T;同时氨气消耗量减少不低于40%,且操作简便,易于实施,易于大规模生产。
一种高磁感取向硅钢脱碳渗氮工艺.pdf
本发明公开了一种高磁感取向硅钢脱碳渗氮工艺,属于取向硅钢制造领域。本发明采用退火炉进行脱碳渗氮,退火炉依次分为预热段‑脱碳段‑渗氮段和冷却段,采用先脱碳再渗氮工艺,在低温湿气氛下首先将碳脱至0.0015%以下;随后在干气氛下进行高温短时渗氮。本发明可以稳定将碳脱至0.0015%以下,渗氮量控制在200~220ppm,初次再结晶平均晶粒尺寸控制在15~20μm,高斯晶粒偏离角在5~8°。本发明有助于解决因渗氮量范围波动大导致磁性能不稳定的问题。
一种用于高磁感取向硅钢渗氮处理的氨气喷管结构.pdf
本发明涉及一种用于高磁感取向硅钢渗氮处理的氨气喷管结构,该氨气喷管结构,包括炉壳、氨气喷管,该氨气喷管可伸进和退出炉壳,该氨气喷管伸进和退出的运动方向与钢带的运动方向垂直,该氨气喷管上设有若干喷气孔,其特征在于:喷气孔斜向对着钢带的运动方向,该喷气孔与氨气喷管中心连线与垂直线呈的夹角为〆,该发明由于采用了喷孔出气方向与带钢运行方向呈一定夹角〆的结构,喷出的氨气与钢带的接触时间长,提供了氨气的分解量,提高了氨气的使用效率和渗氮质量。