
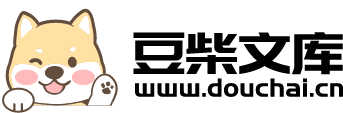
一种烧结钕铁硼永磁材料熔炼用中频感应炉中性炉衬.pdf
羽沫****魔王
在线预览结束,喜欢就下载吧,查找使用更方便
相关资料
一种烧结钕铁硼永磁材料熔炼用中频感应炉中性炉衬.pdf
一种烧结钕铁硼永磁材料熔炼用中频感应炉中性炉衬,使用的原料以高铝质铝矾土熟料为主,加入镁砂粉和外加剂,按比例混合、搅拌均匀,经打结、烘炉而制成。本发明所得中性炉衬具有高耐火度、优异的化学性质稳定性和体积稳定性、耐热冲击性好、筑炉简便快捷,烘炉时间短、炉龄长、综合成本低等特点。
中频感应炉炉衬烧结工艺的改进.docx
中频感应炉炉衬烧结工艺的改进中频感应炉炉衬烧结工艺的改进中频感应炉作为一种广泛使用的加热设备,在工业生产中有着广泛的应用。而其中的炉衬也是产生很大问题的一部分。炉衬在高温下工作,长时间的使用会使其损耗严重,加之生产环境的要求越来越高,导致了高温环境下的恶化现象。因此,对炉衬的选择及烧结工艺的改进显得十分重要,以保证中频感应炉的稳定性和效率。一、中频感应炉炉衬的常见问题在使用中频感应炉的过程中,炉衬的状况通常是人们关注的话题。炉衬作为中频感应炉内部最重要的部件之一,长时间的使用会导致其出现的各种问题。常见的
一种金属熔炼用中频感应炉.pdf
一种金属熔炼用中频感应炉,从外层至内层依次包括炉壳体、感应线圈、石棉布层、石英砂材质的炉胆,感应线圈与炉壳体之间留有间隙,石棉布层和炉胆之间的间隙中设有至少一层玻璃纤维布层;炉壳体包括炉盖和炉盖下方的炉身,炉盖的直径大于炉身的直径,炉盖上设有出液口,出液口下方连通有与炉身平行的导流板;炉身上设有用于支撑导流板的加强筋,加强筋的形状与导流板的下底面形状相适配。本发明提供的金属熔炼用中频感应炉能有效提高中频感应炉的使用寿命,还利于提高炉胆的保温效果,利于提高生产效益及产品质量。
一种烧结钕铁硼永磁材料的烧结方法.pdf
本发明涉及一种烧结钕铁硼永磁材料的烧结方法,包括:(1)将烧结钕铁硼生坯装入烧结炉,抽真空后开始加热,从室温升温至200~400℃,保温0.5~2h;然后继续升温至500~900℃,保温2~8h;(2)步骤(1)保温结束后,升温至低于最佳烧结温度10~30℃的温度下保温4~8h;然后在最佳烧结温度下保温0.5~2h,最后冷却即可。本发明通过在液相烧结收缩时引入新的烧结方法,抑制固相烧结和晶粒长大,确保磁体的晶粒细化,从而使得矫顽力得到确定的提高;方法简单,成本低,具有良好的市场应用前景。
一种熔炼球化剂、孕育剂用中性炉衬材料.pdf
本发明的目的在于提供一种防挂渣、耐压强度高、机械性能好、使用寿命长的熔炼球化剂、孕育剂用中性炉衬材料。本发明提供一种熔炼球化剂、孕育剂用中性炉衬材料,包括骨料和细粉材料,所述骨料包括刚玉颗粒66?88wt%;所述细粉材料包括以下组分:刚玉细粉5?15wt%、氧化铝粉6?16wt%、1?0mm镁砂5?20wt%、添加剂0.2?1.5wt%,所述骨料和细粉材料分别预混后一起混合形成干粉料装袋。