
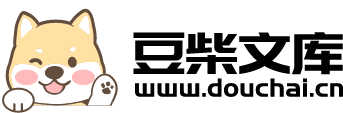
一种转炉炼钢用预熔型脱磷剂的制备方法.pdf
Wi****m7
在线预览结束,喜欢就下载吧,查找使用更方便
相关资料
一种转炉炼钢用预熔型脱磷剂的制备方法.pdf
本发明公开了一种转炉炼钢用预熔型脱磷剂的制备方法,所述脱磷剂以重量份计由下列组分组成:Fe2O320-24份,CaO42-46份,Al2O36-8份,SiO25-9份,Na2CO32-4份,B2O34-8份;所述的制备方法包括如下步骤:1)按上述配比称量配料;2)预熔处理,将配比好的上述组分放入加入炉中,升温至1300-1350℃,待全部组分熔融后,搅拌均匀并再持续熔融20-30分钟,然后自然冷却;3)破碎,将冷却后的预熔料破碎至小于1mm;4)球磨处理,将破碎后的预熔料放入球磨机中,球磨至-40目;5)
一种转炉炼钢用预熔型脱磷剂.pdf
本发明公开了一种转炉炼钢用预熔型脱磷剂,所述脱磷剂以重量份计由下列组分组成:Fe2O320-24份,CaO?42-46份,Al2O36-8份,SiO25-9份,Na2CO32-4份,B2O34-8份;所述脱磷剂为上述组分预熔后制备的粉料,粉料粒度为-40目。
一种新型炼钢用预熔型脱磷剂及其制备方法.pdf
本发明一种新型炼钢用预熔型脱磷剂及其制备方法,目的是提供一种高效的适合炼钢用预熔型脱磷剂,克服上述各种转炉炼钢脱磷材料存在的缺陷。本发明所述预熔型脱磷剂其组成及质量百分比为:CaO:25%~40%,Fe2O3:45%~65%,BaO:0.1~10%其它杂质(MgO\Al2O3\SiO2)≤5.0%。以上各组分质量百分比之和为100%;此预熔渣料粒度为1~100mm。本发明预熔渣的成分均匀稳定性好,具有低熔点(1210℃~1260℃),粘度适宜(1400℃时,0.01~0.05Pa·S),流动性好,熔化速度
一种炼钢用铁钙质预熔型脱磷剂及其制备方法.pdf
本发明涉及一种低成本炼钢用铁钙质预熔型脱磷剂及其制备方法,该脱磷剂的生产原料主要是采用富含氧化钙、氧化铁的工业废弃物。其制备方法是:先将这些工业废弃物制成粉末,再按一定比例混合,然后加入高温窑炉中,熔炼温度1450~1600℃,熔融出炉后,结晶冷却,经破碎,制成富含CaO和Fe2O3、粒度为0~70mm的块状低熔点铁钙质预熔型脱磷剂。该脱磷剂,熔点低、熔速快,在炼钢过程中加入,可促进化渣和脱磷,缩短冶炼时间;由于该脱磷剂经高温熔融而成,成分均匀、性能稳定、不变质、不吸水、不粉化、低氟,不仅便于储存和运输,
转炉炼钢脱磷剂制备方法.pdf
本发明涉及一种转炉炼钢脱磷剂及其制备方法,其特征在于:转炉炼钢脱磷剂是由下列原料按重量百分比组成:三氧化二铁Fe2O3?40%~45%、氧化钙CaO?45%~50%、三氧化二铝Al2O3?1%~4.0%、二氧化硅SiO2<5.0%、氟CaF2?0~1.5%其熔点为低于1150℃。其制备方法为:将上述原料经破碎,混合均匀后,在1200℃~1550℃高温下熔炼,熔化反应生成铁酸钙;在其冷却后,将生成的铁酸钙加工成3~40mm粒块作为实用的转炉脱磷剂。本发明转炉炼钢脱磷剂,具有脱磷效果稳定,消耗低,它能使钢中磷