
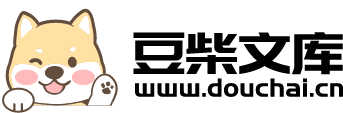
一种耐低温高强度弹簧钢及其制备方法.pdf
慧颖****23
在线预览结束,喜欢就下载吧,查找使用更方便
相关资料
一种耐低温高强度弹簧钢及其制备方法.pdf
本发明公开了一种耐低温高强度弹簧钢及其制备方法,含有的化学成分及其重量百分比为:C0.45-0.55%、Si1.0-1.3%、Mn1.2-1.4%、Ni3.5-5.5%、Cr0.8-1.0%、Cu0.3-0.5%、Ti0.006-0.008%、Zn0.03-0.06%、Sn0.004-0.005%、P≤0.025%、S≤0.025%、余量为铁。制备方法:(1)熔炼、合金化;(2)精炼剂炉外精炼,浇铸、铸后热处理。本发明通过对合金成分进行合理调整,合理设置配比和生产工艺,合理设置投放次序,形成的弹簧钢具有优
一种高强度耐腐蚀弹簧钢及其制备方法.pdf
本发明提供一种高强度耐腐蚀弹簧钢及其制造方法。从弹簧钢满足汽车工业发展需求方向出发,对现有弹簧钢组分进行调整,通过适当降低C含量,增加Si含量,并加入微量元素Nb、Ni和RE,同时,全流程不采用铝质脱氧剂、采用硅铁合金和部分稀土合金以及铬铁合金在转炉出钢过程脱氧合金化,并在LF精炼工艺加入镍铁、铌铁合金进行合金化,RH精炼破空后加入其余稀土合金,热处理工艺采用调整后的淬火+回火工艺,制备得到的高强度耐腐蚀弹簧钢具有良好抗耐腐蚀性能和突出的力学性能,其抗拉强度≥2100MPa,面缩率≥45%,周浸率≤20%
一种高强度耐低温叉车门架型钢及其制备方法.pdf
本发明提供一种高强度耐低温叉车门架型钢及其制备方法,所述叉车门架型钢按重量百分比由以下成分组成:C:0.15%~0.20%、Si:0.35%~0.50%、Mn:1.40%~1.60%、P≤0.020%、S≤0.010%、V:0.07%~0.09%、Nb:0.025%~0.04%、Cr:0.30%~0.45%、N:0.011%~0.016%、O≤0.003%,其余为铁和不可避免的杂质。其制备方法为:转炉冶炼,LF精炼,连铸,钢坯加热,轧制,轧后冷却。本发明制备的叉车门架型钢,成本经济合理,在保证材料较高屈服
一种具有高塑性的超高强度弹簧钢及其制备方法.pdf
本发明涉及一种具有高塑性的超高强度弹簧钢的制备方法,所述方法包括:在设计弹簧钢合金成分时,是在55SiCr钢种的基础上添加适量的合金元素V和Nb,使弹簧钢中V含量为0.1‑0.25wt%,Nb含量为0.005‑0.03wt%;在热处理工艺中,先对弹簧钢工件进行奥氏体化处理,然后进行锡浴低温等温淬火处理,而锡浴低温等温淬火的条件为:等温淬火炉加热至235‑250℃,将奥氏体化处理的弹簧钢工件置于等温淬火炉中,等温淬火炉采用锡浴,淬火速度为200‑300℃·s
一种高强度耐低温热轧叉车门架用槽钢及其制备方法.pdf
本发明提供了一种高强度耐低温热轧叉车门架用槽钢及其制备方法。根据本发明的叉车门架用槽钢的化学成分的重量百分数为:C0.15%~0.20%、Si0.30%~0.45%、Mn1.30%~1.45%、P≤0.025%、S≤0.015%、V0.07%~0.09%,其余为铁和不可避免的微量杂质。根据本发明的叉车门架用槽钢的制备方法包括:铁水预脱硫,控制脱硫后铁水中的硫含量不超过0.020wt%;转炉冶炼,采用顶底复吹转炉冶炼,并且在转炉冶炼过程中,采用铝锰铁脱氧,控制钢水中的氧含量小于30ppm;LF精炼,精炼过程