
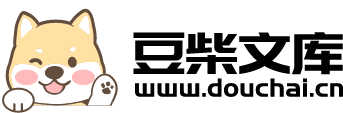
一种硼化锆/碳化硅陶瓷材料的制备方法.pdf
明轩****la
在线预览结束,喜欢就下载吧,查找使用更方便
相关资料
一种硼化锆/碳化硅陶瓷材料的制备方法.pdf
本发明提供了一种硼化锆/碳化硅陶瓷材料的制备方法,先取硫酸铜、四硼酸钠、硼化锆混合,在600~950℃下熔炼,将融熔物放入水中淬火,粉碎淬火产生的块状物,得到粉体I;再将硫酸镁、磷酸铵、碳化硅混合,在1000~1200℃下于马弗炉中烧结,放冷,取出,得到粉体II;最后将粉体I、粉体II、N,Nˊ?亚甲基双丙烯酰胺、聚乙二醇6000、聚乙烯亚胺、柠檬酸胺混合,球磨,加入过硫酸铵、N,N,Nˊ,Nˊ?四甲基乙二胺,搅拌,固化,烧结,冷却,即得。本发明所得的硼化锆/碳化硅陶瓷材料具有良好的力学性能,常温下的断裂
改性硼化锆隔热纳米陶瓷材料的制备方法.pdf
本发明公开了改性硼化锆隔热纳米陶瓷材料的制备方法,该工艺利用螺杆式搅拌桨搅拌、真空反应炉加压高温反应、双螺杆挤出机造型制得纳米陶瓷材料母料,然后利用吸附、超声振荡和蒸发析出三者的平衡作用,使硼化锆吸附于纳米陶瓷材料母料表层得到改性硼化锆隔热纳米陶瓷材料。制备而成的改性硼化锆隔热纳米陶瓷材料,其隔热性能好、抗压抗拉能力强,具有较好的应用前景。
一种硼化锆-碳化硅复合粉体及其制备方法.pdf
本发明涉及一种硼化锆-碳化硅复合粉体及其制备方法。其技术方案是:将1~9wt%的锆英石粉、1~9wt%的金属镁粉、2~10wt%的四硼酸钠粉、0.1~0.9wt%的碳粉和75~91wt%的卤化物粉混合,再将混合粉置入管式电炉,在氩气气氛下以2~8℃/min的速率升温至1100~1300℃,保温2~6小时;然后将所得产物放入浓度为2.0~4.0mol/L的盐酸中浸泡3~8小时,过滤,用去离子水清洗过滤后产物至清洗液中用硝酸银检测无沉淀产生,干燥,得硼化锆-碳化硅复合粉体。本发明具有反应温度低、成本低、工艺简
一种硼化锆-碳化硅复合粉体及其制备方法.docx
一种硼化锆-碳化硅复合粉体及其制备方法一种硼化锆-碳化硅复合粉体及其制备方法一、研究背景硼化锆-碳化硅复合材料具有高硬度、高耐磨性、高温稳定性等优良的物理化学性能,因此被广泛应用于制造高速加工刀具、陶瓷刀具等领域。然而传统的制备方法中存在着设备成本高、工艺复杂等问题,因此需要寻找更加简便、经济且有效的制备方法。二、研究内容本研究旨在提出一种简便经济的硼化锆-碳化硅复合粉体制备方法,并对其进行性能测试评估。三、制备方法1、实验材料准备本实验采用粉末冶金法制备硼化锆-碳化硅复合粉体,需准备的实验材料包括:硼化
一种硼化锆粉末的制备方法.pdf
本发明公开了一种硼化锆粉末的制备方法,包括以下步骤:a、将B粉置于内壁涂有BN粉末的石墨坩埚中,再一同置于氢气还原炉还原;b、将Zr粉置于内壁涂有BN粉末的石墨坩埚中于氢气中还原;c、将步骤a和步骤b制得的B粉和Zr粉按摩尔比为1∶1或者2∶1或者12∶1的比例球磨;d、将球磨后的物料干燥;e、在压强为10~30GPa的条件下,以0.5~30℃/min的升温速率升温到800~2400℃,烧结0.5~8小时;f、将硼化铬块体破碎后过40~60目筛网;g、将制得的硼化铬颗粒球磨、筛分。采用本发明的方法能制备出