
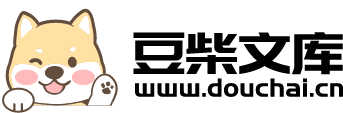
一种制备软磁合金筒形件的旋压成形方法.pdf
书生****瑞梦
亲,该文档总共11页,到这已经超出免费预览范围,如果喜欢就直接下载吧~
相关资料
一种制备软磁合金筒形件的旋压成形方法.pdf
本发明公开了一种制备软磁合金筒形件的旋压成形方法;根据塑性变形过程材料体积不变原理,按照薄壁筒形零件的实际壁厚,并结合成形后的修边需要,按壁厚减薄率为40%~80%的设计原则确定筒形毛坯几何尺寸;将管坯加热至700℃,保温0.5h进行预先热处理;对筒形毛坯进行多道次错距旋压变形,使壁厚减薄达到预期值;在真空保护中将旋压件升温至1100℃~1180℃,保温3h~6h,然后以不大于200℃/h的速度冷却到600℃,再以不小于400℃/h的速度继续冷却至200℃后出炉,进行最终热处理以提高材料的磁性能;切除工件
一种筒形件旋压成形旋轮轨迹设计方法.pdf
本发明涉及旋压设计领域,尤其涉及一种筒形件旋压成形旋轮轨迹设计方法,包括的步骤有:一、以芯模、坯料为研究对象,根据芯模尺寸、坯料尺寸及芯模与坯料之间的装配关系确定旋轮轨迹的起点位置;二、选择渐开线轨迹作为曲线轨迹,并确定曲线参数;三、计算各道次旋轮轨迹及长度,计算间隙补偿量,对旋轮轨迹进行优化;四、将优化后的旋轮轨迹离散成点坐标形式,导入数控旋压机床代码;五、在数控旋压机床上对坯料进行试制,成功即可量产,失败的话返回步骤二,重新确定曲线参数,直至试制成功。本发明的有益效果是:建立了旋轮轨迹,能够对间隙量进
一种薄壁筒形件强力旋压成形装置.pdf
一种薄壁筒形件强力旋压成形装置,它涉及一种旋压成形装置,具体涉及一种薄壁筒形件强力旋压成形装置。本发明为了解决薄壁圆筒件壁厚尺寸和形状尺寸精度要求高,厚壁管加工切削量大,加工效率低,材料利用率低的问题。本发明包括旋压轴、旋压轴驱动组件和三个旋压轮,三个旋压轮呈等边三角形安装在旋压轮固定架上,旋压轴的一端设置在三个旋压轮所组成的等边三角形的几何中心,旋压轴的另一端通过所述旋压轴驱动组件与机床主轴连接盘连接。本发明属于机械加工领域。
带环向内加强筋筒形件旋压成形方法.pdf
本发明提供一种带环向内加强筋筒形件旋压成形方法,该方法包括如下步骤:1、采用卷板焊或挤压管材机加的方法制造结构简单的旋压毛坯,在毛坯端面预留厚度6mm左右,直径比毛坯外径大12mm左右的工艺环;2、通过退火处理消除毛坯内应力;3、采用压料环将毛坯固定在模具内,通过旋轮压下量、进给速度等参数的合理选取实现材料正向旋压,使毛坯逐点减薄并拉长,在此过程中,通过旋轮与旋压模具间隙的调整实现加强筋的成形;4、通过车削加工切去长度方向余量,使旋压后半成品达到产品长度要求。本发明的提供的成形方法中材料利用率高,成型过程
一种大直径钛合金筒形件的热旋压成形方法.pdf
本发明属于钛筒形件的塑性成形技术领域,涉及一种大直径钛合金筒形件的热旋压成形方法,将坯料放置在电阻炉中进行加热,待温度达到600~650℃,保温0.5~1h后取出;坯料内径尺寸因受热后膨胀变大,将坯料热装到芯模后,待坯料与芯模之间的最大间隙小于0.5mm时开始旋压,芯模和旋轮无需预热,采用多道次的旋压工艺,使坯料变形更加均匀。本发明采用立式旋压机进行旋压,具有芯模更换方便、坯料装拆简单的特点,可用于外径3m以上的钛合金筒形件的热旋压成形,所获得的筒形件直线度和圆度较好,可满足大直径高端生箔阴极辊表面的钛筒