
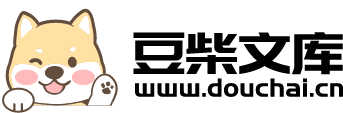
一种铜杆生产用溜槽装置及铜杆制造方法.pdf
瀚玥****魔王
在线预览结束,喜欢就下载吧,查找使用更方便
相关资料
一种铜杆生产用溜槽装置及铜杆制造方法.pdf
本发明提供一种铜杆生产用溜槽装置及铜杆制造方法,所述溜槽装置具有预设的倾角,包括依次连接的内部形成有铜液流通通道的旋转溜槽、弯溜槽、直溜槽,其中所述旋转溜槽连接于熔化炉的后方,弯溜槽以预设的水平转角连接于旋转流道的后方,使得在熔化炉带动旋转溜槽摆动时,由熔化炉流入旋转溜槽的铜液流入弯溜槽、直溜槽,并且在溜槽装置上间隔设置有多个烧嘴,通过烧嘴通入溜槽装置内的可燃气体与空气预混燃烧,对流入的铜液进行还原、保温,避免铜液氧化。该溜槽装置采用几段溜槽连接而成,且各个溜槽又由多个预制块拼接而成,并在浇筑料外侧贴装多
一种生产铜杆的方法及铜杆拉丝装置.pdf
本发明公开了一种生产铜杆的方法,包括以下步骤:1)熔铜工序:将铜板融化成熔融铜;2)铸杆工序:将所述熔融铜铸造于芯杆的表面生成铸杆;3)热轧工序:将冷却后的所述铸杆进行热轧处理生成铜杆;4)绕制工序:将上述铜杆绕制成圈;其中,所述铸杆工序包括铜杆拉丝操作,采用铜杆拉丝装置将铜杆拉制成芯杆,所述铸杆工序包括铜杆拉丝操作,所述铜杆拉丝操作采用铜杆拉丝装置将铜杆拉制成芯杆,并通过循环的氦气将拉丝炉一侧的热量传递至绞盘中,同时利用冷却油对绞盘进行降温。本发明解决了现有技术中直接对绞盘用冷却水进行降温,高温铜杆进入
一种铜杆生产用密闭式预热炉及铜杆制造方法.pdf
本发明提供一种铜杆生产用密闭式预热炉及铜杆制造方法,该预热炉包括:燃烧室,燃烧室内设置有多个用于对铜料进行预热的烧嘴;连接室,连接室将燃烧室和熔化炉密闭连接;输送装置,输送装置将铜料输送入燃烧室,并将预热后的铜料输送至熔化炉。本发明采用密闭式输送铜料,可有效保证炉内温度,使铜料达到300℃要求,减少热能损失;将现有技术中的履带式输送带变为辊道式输送带,增大受力强度,不易变形,损坏,节省维修强度;更改烧嘴的位置,使燃烧室内的热能分布更合理,提高热效率。
一种铜杆浸涂系统及铜杆生产方法.pdf
本发明公开了一种铜杆浸涂系统,包括:设置有第一通道的熔化炉、通过第一通道与熔化炉相连通的保温炉以及与保温炉相连通的浸涂室;保温炉设置有第二通道,浸涂室通过第二通道与保温炉相连通;熔化炉的炉体设置有炉体倾斜设备;保温炉设置有气体控制设备、高温块以及与高温块相连接的第一驱动装置,高温块置于保温炉的炉腔内且可沿着竖直方向运动。本发明同时还提供了一种铜杆生产方法,包括浸涂工序,通过采用上文所述的铜杆浸涂系统将芯杆涂覆成铸杆;冷却工序,将所述铸杆进行冷却;热轧工序,将冷却后的所述铸杆进行热轧处理生成铜杆;绕制工序,
一种铜杆生产装置.pdf
本发明涉及铜杆生产技术领域,尤其涉及一种铜杆生产装置,包括混合阀、制氧机和熔化炉及天然气发生装置,制氧机、天然气发生装置和熔化炉分别与混合阀相连通,制氧机产生的氧气与天然气发生装置输送的天然气进入到混合阀内内进行混合,混合后的燃气从混合阀内喷出到熔化炉内,进入熔化炉内的混合后的燃气被点燃用于熔化废铜。用制氧机进行氧气制备,制备的氧气浓度为93%,以此来替代氧气瓶的使用,在实际实际使用过程中与可以达到97%浓度的氧气瓶的使用效果,使得铜杆生产过程中废铜回收的成本降低。