
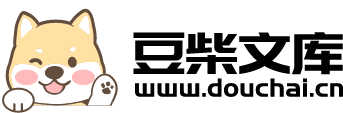
一种大型卸扣的整体锻造方法.pdf
猫巷****婉慧
在线预览结束,喜欢就下载吧,查找使用更方便
相关资料
一种大型卸扣的整体锻造方法.pdf
本发明公开了一种大型卸扣的整体锻造方法,涉及卸扣技术领域。本发明包括以下步骤:SS01下料:根据要求对原材料化验、分析并下料,SS02锻造:在加热炉内加热,采用锻压设备将锻件锻造成圆棒状,并将两端压扁,SS03车加工:将圆钢两端铣出平面,其余部位车圆,SS04折弯成型:在加热炉内加热后进行折弯处理,SS05表面处理:对成品进行打磨修整,SS06成品检测,SS07入库。本发明通过在成品形状不影响承载力的条件下,将卸扣本体设为由一组平直部、一组环形部和一弧形连接部组成的形状特征,生产时采用锻圆棒、两端压扁、两
Y型卸扣的锻造方法.pdf
本发明公开了一种Y型卸扣的锻造方法,其包括以下步骤:步骤一,下料,根据要求的产品尺寸确定所需圆钢尺寸;步骤二,加热,将圆钢放入火焰炉内加热;步骤三,拔长,用电液锤将加热的圆钢反复镦粗拔长;步骤四,打方、分料,锤头敲击一端并整形,以达到要求制坯尺寸,对达到制坯尺寸的毛坯产品进行分料,对一端进行拔长,对拔长后的毛坯件进行分料,对一端进行拔长;步骤五,打磨修整,对成型后的锻件进行打磨修整,去除应力敏感区,并修整到要求尺寸。本发明锻造出的Y型卸扣具有良好的力学性能和高强度、强韧性的技术特征,且满足尺寸和形状要求。
一种小型D卸扣的自动化锻造方法.pdf
本发明公开一种小型D卸扣的自动化锻造方法,包括卸扣本体,包括以下步骤:(1)下料;(2)卸扣两端镦粗成型;(3)卸扣两头拍扁与冲孔;(4)卸扣折弯;(5)卸扣整形;(6)打磨;(7)探伤;本发明减少了返工率,在锻造时节省了人力和时间,同时降低了成本,也提高了工作效率。
一种R5级系泊链附件旋转卸扣的锻造方法.pdf
一种R5级系泊链附件旋转卸扣的锻造方法,根据图纸设计要求对原材料进行落料;用探伤仪对材料进行无损检测;在箱式反射炉内进行加热;锻造温度控制在900-1100℃;用3吨皮带锤,分别将锻件打成长方体、两端锻打成台阶、在锻件中放入成型模具,锻造成型;回火,将锻件放在回火炉内,回火温度控制在620-650℃;用探伤仪对锻件进行无损检测。本发明适当提高了R5级系泊链附件旋转卸扣的始锻温度和终锻温度,另外由于R5级旋转卸扣锻造时会产生表面裂纹,所以同时也适当提高了锻造温度,增加了锻件机加工余量,达到了船级社对R5级系
JB_8112-1999_一般起重用锻造卸扣D形卸扣和弓形卸扣.pdf