
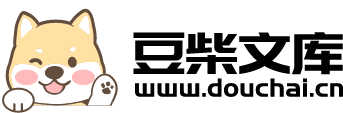
高钛型高炉渣选铼的方法.pdf
努力****承悦
在线预览结束,喜欢就下载吧,查找使用更方便
相关资料
高钛型高炉渣选铼的方法.pdf
本发明属于冶金渣回收利用技术领域,具体涉及一种高钛型高炉渣选铼的方法。针对现有缺乏一种能够有效分离高炉渣中铼和其他杂质的方法,无法回收高炉渣中铼的问题,本发明提供了一种高钛型高炉渣选铼的方法,包括以下步骤:a、将高钛型高炉渣静置30~60min,缓慢倒出上层渣液,保留20~30%的渣;b、将渣用中频炉冶炼,倒出铁,留下的渣液冷却、沉淀,再次得到罐底渣;c、将罐底渣用硫酸洗涤,净化,再采用离子交换树脂洗脱,得到铼溶液,再经第二次净化,浓缩,采用氢气还原,得到高纯铼粉。本发明首次提供了一种从高钛型高炉渣选铼的
高钛型高炉渣中选钛的方法.pdf
本发明公开了一种高钛型高炉渣中选钛的方法,尤其是一种用于废弃资源回收利用领域的高钛型高炉渣中选钛的方法。本发明提供一种能够有效的将高钛型高炉渣中的其它杂质和二氧化钛分离,从而大幅提高二氧化钛的品位,使高钛型高炉渣中的二氧化钛得到合理利用的高钛型高炉渣中选钛的方法,包括以下几个步骤:A、将高钛型高炉渣放入二段球磨机中进行球磨处理;B、对球磨处理后的高钛型高炉渣进行强磁磁选处理;C、对强磁磁选处理后的高钛型高炉渣进行浮选处理。本申请采用了先磁选再浮选的处理步骤,对处理设备进行了合理处理,并大幅提高二氧化钛的品
高钛型高炉渣的回收利用方法.pdf
本发明属于冶金固废资源综合利用技术领域,具体公开了一种高钛型高炉渣的回收利用方法,旨在解决如何回收利用高钛型高炉渣的显热资源的问题。该高钛型高炉渣的回收利用方法,通过利用铸渣板将温度在1200~1350℃的液态高钛型高炉渣铸造为900~1000℃的高温渣块,再将高温渣块间歇式加入换热罐中通过换热罐内由下往上流动的冷风进行换热;换热后,冷风变为热风并用于发电设备发电或物料干燥,可使得高钛型高炉渣的显热资源得到充分回收利用,利用率达到40%以上。
高钛型高炉渣制备除锈砂的方法.pdf
本发明属于冶金渣回收利用技术领域,具体涉及一种高钛型高炉渣制备除锈砂的方法。针对现有采用高钛型高炉渣制备除锈砂强度低、粒径不均匀的问题,本发明提供一种高钛型高炉渣制备除锈砂的方法,包括以下步骤:a、将熔融的高钛型高炉渣用压缩空气进行风淬;b、对风淬后的高钛型高炉风淬渣进行分选;c、将粒径≤2mm的风淬高钛型高炉渣与石英砂按重量比7~8︰2~3进行混合,制成高钛型高炉渣除锈砂。本发明制备除锈砂的方法操作简单,效果好,制备得到的除锈砂比传统的除锈砂粒径更均匀,除锈效果更好;可有效的去除油污、油脂、残留氧化皮、
利用高钛型高炉渣制备钛铝合金的方法.pdf
本发明提供了一种利用高钛型高炉渣制备钛铝合金的方法,该方法首先通过电渣重熔步骤,以铝作为自耗电极还原高钛型高炉渣中的钛、硅等元素的氧化物,制得钛硅铝合金再将钛硅铝合金制棒,进行区域熔炼,将硅元素等杂质区分切除,最后得到钛铝合金。本发明方法不仅解决了高钛型高炉渣堆放引起的环境污染问题,还防止宝贵的钛资源流失,具有钛元素回收率高,设备、工艺成本低,附加产值收益高的优点,适于工业化加工生产。?