
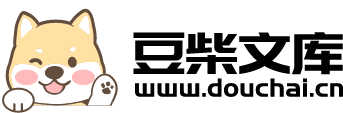
一种高强度耐磨钢及其制备方法.pdf
St****12
在线预览结束,喜欢就下载吧,查找使用更方便
相关资料
一种高强度耐磨钢及其制备方法.pdf
本发明公开了一种高强度耐磨钢,化学组成以重量百分比计包含C:0.41‑0.59%、Si:0.31‑0.58%、Mn:7.1‑8.9%、P≤0.018%、S≤0.01%、Ti:0.25‑0.35%,Cr:3.60‑5.60%、Zr:0.10‑0.30%,余量为Fe和不可避免的杂质;该钢的微观组织由10‑20%奥氏体和回火马氏体构成。同时,本发明还公开了一种该耐磨钢的制备方法,采用的工艺路线包括:转炉冶炼→钢包炉精炼→模铸→锻造→轧制→轧后冷却→热处理。该耐磨钢具有较高的屈服强度和优良的耐磨性能。采用该耐磨钢
耐磨、高强度高速工具钢及其制备方法.pdf
本发明属于一种耐磨、高强度高速工具钢,其特征在于按重计,铁,碳,锰,磷,硫,铬,钴,钼,钨,钒,氮,氧,氢,氩。耐磨、高强度高速工具钢的制备方法,采取以下步骤:a、取750份铁,将其中的500份铁投入中频感应炉(1)中冶炼;b、将钢条用电击棒抛光机(2)进行抛光;c、把抛光后的钢条放入真空冶炼炉(3)冶炼;d、经真空处理后的钢条放入电渣炉(4)中进行电渣处理;e、将电渣处理后制成的钢锭放到真空退火炉(5)中进行退火;f、最后放到热处理炉(6)中热处理三次。本发明的有益效果是:该发明耐磨性、耐热性能好,表面
履带板用高强度耐磨钢及其制备方法.pdf
履带板用高强度耐磨钢及其制备方法属于冶金技术。主要是为解决现有的履带板用钢普遍存在屈服强度、抗拉强度及硬度都低,耐磨性差的问题而发明的。所述的履带板用高强度耐磨钢的化学成分重量百分比为:C0.21%—0.26%、Si0.15%—0.30%、Mn0.80%—1.20%、P≤0.03%、S≤0.015%、B0.0005%—0.003%、Cr0.30%—0.50%,其余为铁和微量杂质。制备方法包括如下步骤:铁水接收;电炉冶炼;出钢合金化;LF?精炼;VD真空处理;连铸;轧制。优点是屈服强度、抗拉强度及硬度高,耐
一种耐磨钢球及其制备方法.pdf
一种耐磨钢球及其制备方法,属于耐磨材料技术领域。所述耐磨钢球以废旧弹簧钢、废旧碳化硅、废旧硅钢片和氮化铬铁为主要原料,其加入量分别占进入炉内炉料质量分数的88.2‑88.5%、1.2‑1.3%、8.2‑8.4%、2.1‑2.3%。采用电炉熔炼钢水,用连铸机连铸成圆钢坯,经轧制和定尺锯断成圆钢棒,再在轧球生产线上轧制成钢球,经淬火和回火热处理后即可获得力学性能优异耐磨钢球,具有成本低廉、低破碎率和低磨损率等优势,推广应用具有良好的经济和社会效益。
双相耐磨钢及其制备方法.pdf
本发明公开了一种双相耐磨钢及其制备方法,它包括双相耐磨钢的基体组织为铁素体与马氏体双相结构,两者体积分数占比分别为:4%~7%、93%~96%,且两种基体中均弥散析出(Nb、Ti、Mo、RE)C纳米颗粒,且粒径<10nm的(Nb、Ti、Mo、RE)C纳米颗粒占30%以上;包括按照原料化学成分及其重量百分比,准备冶炼所需的原料,将原料进行冶炼,获得冶炼钢液;将冶炼钢液进行板坯连铸,获得坯料;将坯料放置在加热炉中加热,并进行粗轧和精轧;轧后采用层流冷却,并对冷却后的钢板进行热处理。本发明通过在铁素体+马氏体双