
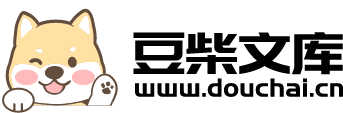
一种高温烟气脱硝催化剂及其制备方法.pdf
一条****发啊
在线预览结束,喜欢就下载吧,查找使用更方便
相关资料
一种高温烟气脱硝催化剂及其制备方法.pdf
本发明公开了一种高温烟气脱硝催化剂及其制备方法。本发明所述的催化剂以燃煤电厂固体废弃物粉煤灰为载体,以赤泥提取的三氧化二铁为活性组分,经等体积浸渍、干燥、煅烧和粉碎制得。本发明的催化剂具有比表面积大、脱硝效率高、高温稳定性强等优点,在烟气温度为450~550℃的温度区间内可保持脱硝活性90%以上,特别适合于垃圾焚烧锅炉、燃气轮机和柴油内燃机等工业设备的高温尾气脱硝。
烟气脱硝催化剂及其制备方法.pdf
本发明涉及环境保护与催化技术领域,公开了一种烟气脱硝催化剂及其制备方法,将铁盐、草酸、锰盐、纳米二氧化钛和水混合得到浆液,然后依次进行蒸发浸渍和干燥得到成型前粉体,再和成型助剂进行干混,加水混合,将得到湿料团挤出成型,然后进行干燥和煅烧制备得到催化剂成品。本发明的烟气脱硝催化剂的挤条成型工艺流程简单、环保、成本低,制备出的催化剂具有优异的脱硝性能和抗硫中毒能力,适用于工业锅炉、水泥窑炉等低温烟气的处理,同时可用于制备蜂窝式催化剂。
一种中高温烟气脱硝催化剂的制备方法及其应用.pdf
本发明涉及环境保护中氮氧化物控制技术领域,具体涉及一种应用于煤层气发电厂排放的中高温烟气脱硝催化剂的其制备方法和应用。该脱硝催化剂包括催化剂涂层和蜂窝陶瓷,催化剂涂层载体为介孔二氧化硅分子筛和涂敷型氧化铝,活性成分包括铁元素和/或铈元素,助催化成分包括钼元素、钨元素和钯元素;催化剂涂层经浸渍、烘干和焙烧法涂敷于蜂窝陶瓷得到工业脱硝催化剂,制备完成的蜂窝脱硝催化剂可有效应用于煤层气发电厂排放的中高温烟气脱硝,在500℃温度脱除氮氧化物效率达到99%,无毒且具备优异的耐久性。
一种烟气脱硝催化剂及其制备方法.pdf
本发明涉及一种蜂窝式烟气脱硝催化剂的制备方法,其包括如下步骤:将钛源前驱体溶液、铝源前驱体溶液混合均匀得到混合溶液;调节混合溶液pH值至7~11,沉淀、过滤;将滤饼与强碱溶液混合,搅拌后,沉淀、洗涤、过滤;在滤饼中加入去离子水调成浆状,加入钨源前躯体和/或钼源前躯体溶解形成的前躯体溶液,均匀混合后,干燥、焙烧,研磨成粉体;将粉体与钒源前躯体溶液、高分子分散剂均匀混合后,再加入去离子水、助挤剂、造孔剂、纳米二氧化硅、玻璃纤维、粘结剂,调节pH值至7.3~9.0,均匀混合成膏状,挤出蜂窝式胚体,烘干、焙烧。本
一种锅炉烟气脱硝催化剂及其制备方法.pdf
本发明公开了一种锅炉烟气脱硝催化剂及其制备方法,包括如下质量比成份:70~80份去离子水、5~10份柠檬酸、10~15份硝酸盐、20~40份玻璃纤维、1~3份木棉、100~150份二氧化钛、6~12份金属氧化物活性剂、5~15份结构助剂、50~80复合助剂、2~8份层柱粘土、3~7份油酸、15~25份氨水、10~18份分子筛、1~3份扩孔剂和50~60份氧化剂溶液;本发明通过二氧化钛、复合助剂、油酸、层柱黏土配合锰酸镧、玻璃纤维和木棉构筑催化剂载体,提高其负载性,机械强度更高,且锰酸镧为催化剂载体提供了纳