
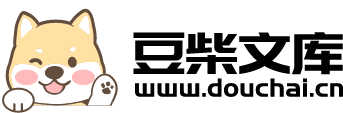
一种单渣深脱硫的转炉炼钢方法.pdf
小忆****ng
在线预览结束,喜欢就下载吧,查找使用更方便
相关资料
一种单渣深脱硫的转炉炼钢方法.pdf
本发明公开了一种单渣深脱硫的转炉炼钢方法,涉及钢铁生产技术领域,铁水占总装入量比例≥80%,对装入转炉铁水进行脱硫、扒渣,脱硫后铁水硫含量≤0.002%;废钢占总装入量比例≤20%,硫含量≤0.020%;上炉冶炼钢水终点硫含量≤0.010%,溅渣后不倒渣,留渣量≥4t;加入废钢铁水后,供氧强度控制在160‑250m
一种转炉炼钢倒渣方法.pdf
本申请实施例提供的转炉炼钢倒渣方法,包括放钢结束,检测模块发倒渣信号,控制模块发原料消耗量和脱磷脱硫条件至炼钢二级静动态模型,炼钢二级静动态模型计算倒渣参数并发至控制模块,确定倒渣模式,为单渣倒渣模式,由倒渣参数设定炉倾角度倒渣和倒渣的参数,放钢结束启动炉倾角度倒渣,控制转炉完成单渣倒渣后,控制转炉溅渣,为双渣倒渣模式,确定为双渣留渣或双渣不留渣模式,冶炼中吹氧后4‑5分钟和放钢结束时,均启动称重倒渣,冶炼中吹氧后4‑5分钟称重倒渣后造渣,控制转炉完成双渣倒渣。炼钢二级静动态模型与倒渣控制结合,由原料消耗
转炉留渣单渣法炼钢工艺试验.docx
转炉留渣单渣法炼钢工艺试验转炉留渣单渣法炼钢工艺试验引言:钢铁是现代工业的基础材料之一,炼钢工艺的改进和创新对于钢铁行业的发展至关重要。转炉留渣单渣法炼钢工艺是一种常见的炼钢工艺,本文将对其进行试验分析和讨论。一、转炉留渣单渣法炼钢工艺概述转炉留渣单渣法炼钢工艺是指在转炉炼钢过程中,将炉渣从转炉中取出,使其成为单独的渣料,并通过特定的工艺对其进行处理和利用。这种工艺的特点是能够有效地减少渣钢之间的相互污染,提高钢水的质量。二、转炉留渣单渣法炼钢工艺试验原理转炉留渣单渣法炼钢工艺试验通过实际操作和观测,来验
一种炼钢转炉降低渣料的方法.pdf
本发明涉及转炉炼钢技术领域,且公开了一种炼钢转炉降低渣料的方法,包括以下步骤:1)在高炉铁水的处理上,采取“一罐到底”的技术手段,更加确实有效地保证高炉铁水的温度和成分,杜绝预处理脱S时渣铁不分,而造成转炉后期处理S的渣料加入的问题;2)严格搭配废钢比,将废钢比维持在18%一下,并控制提钒转炉Sic的加入量,确保C‑T平衡,杜绝使用渣料降温,安排人员,定期取渣样,进行成分的分析,随时了解炉渣成分,及时调整渣料加入,保证转炉冶炼过程的脱P率。该炼钢转炉降低渣料的方法,确保生产顺行、产品质量和炉况受控,将转炉
一种转炉留渣双渣自动炼钢控制方法.pdf
本发明涉及一种转炉留渣双渣自动炼钢控制装置,所述自动炼钢控制装置包括如下控制模块:(1)L2(指转炉过程控制系统)渣计算模块,用于计算炉次留渣量、成分、温度,为下一炉计算提供相关数据;L2数据收集模块,用于收集生产炉次的相关过程数据;L2双渣前期计算模块;L2双渣后期计算模块:根据铁水条件、钢水的目标值等,计算双渣冶炼后期的辅料加入、吹氧量;L1‑L2通信模块;L1辅料加入控制模块,控制辅料的自动称量、加入;L1氧枪控制模块:控制氧枪的自动下枪、提枪以及枪高、氧气流量;L1排渣控制模块:控制转炉排渣操作;