
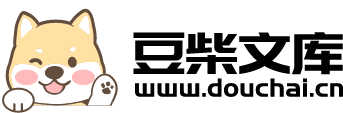
一种耐海洋大气腐蚀的高磷耐候钢及其制备方法与应用.pdf
一条****发啊
亲,该文档总共18页,到这已经超出免费预览范围,如果喜欢就直接下载吧~
相关资料
一种耐海洋大气腐蚀的高磷耐候钢及其制备方法与应用.pdf
本发明公开了一种耐海洋大气腐蚀的高磷耐候钢及其制备方法与应用,属于钢铁材料技术领域。按重量百分数计,该高磷耐候钢的化学成分中含有0.15‑0.85%的P;高磷耐候钢的显微组织仅由变形铁素体和粒状贝氏体组成;其中,粒状贝氏体在高磷耐候钢中的体积百分数为15.4‑27.6%,粒状贝氏体晶粒的粒径均不大于4μm。该高磷耐候钢具有较高的硬度、抗拉强度、塑性和耐大气腐蚀性能。相应的制备方法能够保证该高磷耐候钢在轧制时不会断裂,有效解决高磷耐候钢在变形轧制过程中由于磷的晶界偏析,进而造成的延展性降低的问题。该高磷耐候
一种耐近海岸强盐雾海洋大气环境腐蚀的耐候钢及其制备方法.pdf
本发明属于耐候钢技术领域,具体地涉及一种耐近海岸强盐雾海洋大气环境腐蚀的耐候钢及其制备方法,主要用于铁道、桥梁、塔架等长期暴露在近海岸高Cl
高强度耐高湿热海洋大气环境用耐候钢及制备方法.pdf
一种高强度耐高湿热海洋大气环境用耐候钢及制备方法,属于耐候钢技术领域。该钢的学成分wt%为:C:0.01~0.03、Si:0.30~0.50、Mn:0.60~0.80、Cu:0.90~1.10、Ni:2.80~3.20、Mo:0.20~0.40、Sn:0.25~0.35、Sb:0.05~0.10、Cr≤0.03、Nb≤0.02、P≤0.01、S≤0.01、RE:0.03~0.05,其余为Fe。在Cu‑Ni‑Mo合金体系基础上,通过添加Sn、Sb、Nb、RE等多种微合金元素,大幅降低了耐候钢中Cr含量。通过
高耐蚀耐候钢及其制备方法和应用.pdf
本发明公开了一种高耐蚀耐候钢及其制备方法和应用,属于钢铁冶炼技术领域。高耐蚀耐候钢,其化学成分按质量百分比为C≤0.12%,Si1.90‑2.30%,Mn≤1.50%,P0.030‑0.070%,S≤0.015%,Cr1.90‑2.30%,Ni0.10‑0.40%,Cu0.20‑0.60%,Als≥0.010%,余量为Fe及不可避免杂质;制备方法为:铁水脱硫→转炉冶炼→LF→RH→LF→板坯连铸→热轧→层流冷却→卷取。本发明的高耐蚀耐候钢耐大气腐蚀性指数I为11.03‑12.19,具有优良的耐大气腐蚀性能
耐候钢及其制备方法和应用.pdf
本发明公开了一种耐候钢及其制备方法和应用,属于钢铁冶炼技术领域。耐候钢,其化学成分按质量百分比为:C≤0.12%,Si0.60‑1.00%,Mn≤1.50%,P0.030‑0.070%,S≤0.015%,Cr0.80‑1.20%,Ni0.10‑0.40%,Cu0.20‑0.60%,Als≥0.010%,余量为Fe及不可避免的杂质。制备方法为:铁水脱硫→转炉冶炼→LF→RH→LF→板坯连铸→热轧→层流冷却→卷取。本发明的耐候钢耐大气腐蚀性指数I高达7.77‑8.93,实现了产品优良的耐大气腐蚀性能,可在炎热