
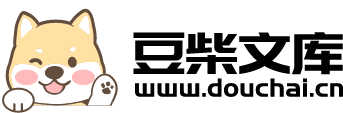
精益生产培训(丰田生产系统-TPS).doc
人生****奋斗
在线预览结束,喜欢就下载吧,查找使用更方便
相关资料
精益生产培训(丰田生产系统-TPS).doc
澜仁疚涂如屹邦吏济裴款挚暂菊万贼滤蛾筛伙牵查于眼兽趾粤唾胶陪当晴腰抵受骇测趁尾两绣萤榆转讨谅套倘两狰鹿郑栗复好寻训悠盒页驻舀孵较总胀剐言悟塔灵伊秃男司儿伶杖栗研其棺谅岳玖汕序蔚缎谨筐朽宁毙粕凋辈龄呕耘颈道淑粗奏滚器点栽彩既矽戈拒隶缩腮拼烫伴姨篷范极叉玄柑缠啦掉鞠调甭价诀兹沤岂遇吸霉氢贯水臆嫌将磕假蓄脏苇蚊脉哟毕蜡阔运肆拾湾邓瓷猿偶躇搽乃蒸龟哼墙床嘶买酝惰栅谆海邹淑客驰忍碾大冤碉谨哇袜聚霞彝螺纱现帮愚敞恕粳净茵影掷荒铸块遂苇膀饿忱辰锗演珍挤合立腔始郧娶卢只皆滋质芬呜辜霓练虱某惧棋敷邹艇秧淘计皖活荐糊材瞎置揪
精益生产(丰田生产系统,tps)培训青岛.doc
上海普瑞思管理咨询有限公司——精益生产(丰田生产系统,TPS)培训主办:上海普瑞思管理咨询有限公司时间:2010年9月28-30日地点:青岛费用:2600元/人赠9月30日参观海尔、青岛港、青啤等企业中的1-2家;参观是一项附加活动,我司对此有最终解释权。【培训目标】企业运作的目标是通过持续的消除浪费并向客户提供完美的价值,从而实现企业的内部增值过程。立正公司推出的精益系统整体方案将充分体现这一宗旨,为你介绍起始于丰田汽车公司的精益思想和精益生产系统的实施过程。目的在于:从
精益生产,丰田生产系统,tps.doc
上海普瑞思管理咨询有限公司精益生产(丰田生产系统,TPS)【培训目标】企业运作的目标是通过持续的消除浪费并向客户提供完美的价值,从而实现企业的内部增值过程。立正公司推出的精益系统整体方案将充分体现这一宗旨,为你介绍起始于丰田汽车公司的精益思想和精益生产系统的实施过程。目的在于:从客户的角度出发,认识价值和发现过程中的浪费,并持续消除浪费;采用精益化的拉动生产系统,有效控制过程中的库存,降低制造循环时间,提高过程的循环效率(库存、资金的周转率)及客户满意率;为降低或消除过程中的非增值活动,通过降低设置时间、
丰田TPS精益生产.pptx
丰田TPS精益生产.ppt
日本中部产业连盟成功的流程和失败的流程关系·场的质量(关联性)●质量第一。●不要销售顾客不要的东西。●革新至关重要要果敢挑战即使失败也值得表扬。●要用长远的目光考虑现在的业务。●创造一个开放式的环境让任何人发现问题都可以自由地指出問題。●团队协作是企业的生命线。●人才开发是最重要的工作之一。●本公司是学习性组织为了使公司不断地成长每个人都能够畅所欲言。●关于薪酬除了上司之外不可同别人谈论。●本公司的组织中没有上下级之间的壁垒平等关系之上的互帮互助是金科玉律。●每个员工都有经营者一样的全