
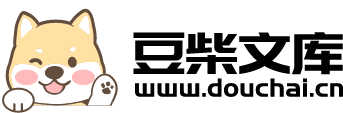
cmk培训更新.doc
傲丝****账号
在线预览结束,喜欢就下载吧,查找使用更方便
相关资料
cmk培训更新.doc
QS9000系列培训资料Revison:A机器能力指数研究—Cmk1.为什么要推行Cmk研究?汽车零件加工最重要的是设备的稳定性工厂按照高生产运行指标购置自动化设备机床不稳定加工质量差频繁停机会影响工厂最终的生存。汽车零件厂选购的设备验收时大多要测试机床的稳定性(Cmk值)或切削过程的稳定性(Cpk值)这不仅是中国汽车厂的要求也是全世界汽车厂的统一要求。Cmk、Cpk值>1.33、1.66或2.0值越高机床运行就越稳定产品质量就越能得到保证。国内好的机床>1.33要>1.66比较困难
cmk培训更新.doc
QS9000系列培训资料Revison:A机器能力指数研究—Cmk1.为什么要推行Cmk研究?汽车零件加工最重要的是设备的稳定性,工厂按照高生产运行指标购置自动化设备,机床不稳定,加工质量差,频繁停机,会影响工厂最终的生存。汽车零件厂选购的设备,验收时大多要测试机床的稳定性(Cmk值),或切削过程的稳定性(Cpk值),这不仅是中国汽车厂的要求,也是全世界汽车厂的统一要求。Cmk、Cpk值>1.33、1.66或2.0,值越高,机床运行就越稳定,产品质量就越能得到保证。国内好的机床>1.33,要>1.66比较
人力资源-2022cmk培训更新.docx
编号:时间:2021年x月x日书山有路勤为径学海无涯苦作舟页码:QS9000系列培训资料Revison:A机器能力指数研究—Cmk1.为什么要推行Cmk研究?汽车零件加工最重要的是设备的稳定性工厂按照高生产运行指标购置自动化设备机床不稳定加工质量差频繁停机会影响工厂最终的生存。汽车零件厂选购的设备验收时大多要测试机床的稳定性(Cmk值)或切削过程的稳定性(Cpk值)这不仅是中国汽车厂的要求也是全世界汽车厂的统一要求。Cmk、Cpk值>1.33、1.
人力资源-2022cmk培训更新.docx
编号:时间:2021年x月x日书山有路勤为径,学海无涯苦作舟页码:QS9000系列培训资料Revison:A机器能力指数研究—Cmk1.为什么要推行Cmk研究?汽车零件加工最重要的是设备的稳定性,工厂按照高生产运行指标购置自动化设备,机床不稳定,加工质量差,频繁停机,会影响工厂最终的生存。汽车零件厂选购的设备,验收时大多要测试机床的稳定性(Cmk值),或切削过程的稳定性(Cpk值),这不仅是中国汽车厂的要求,也是全世界汽车厂的统一要求。Cmk、Cpk值>1.33、1.66或2.0,值越高,机床
人力资源-2022cmk培训更新.docx
编号:时间:2021年x月x日书山有路勤为径学海无涯苦作舟页码:QS9000系列培训资料Revison:A机器能力指数研究—Cmk1.为什么要推行Cmk研究?汽车零件加工最重要的是设备的稳定性工厂按照高生产运行指标购置自动化设备机床不稳定加工质量差频繁停机会影响工厂最终的生存。汽车零件厂选购的设备验收时大多要测试机床的稳定性(Cmk值)或切削过程的稳定性(Cpk值)这不仅是中国汽车厂的要求也是全世界汽车厂的统一要求。Cmk、Cpk值>1.33、1.