
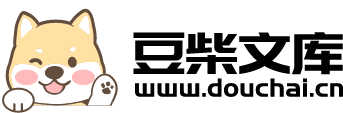
(完整word版)变速箱壳体铸造工艺设计.doc
白凡****12
在线预览结束,喜欢就下载吧,查找使用更方便
相关资料
(完整word版)变速箱壳体铸造工艺设计.doc
5.3.3变速箱壳体铸造工艺设计(1)生产条件变速箱壳体铸件材质HT200,铸件质量82kg,外形尺寸552.5mm×513mm×488.2mm,壁厚10~30mm,主要壁厚10mm,如图5.3-9。采用5t/h倒大双热风冲天炉熔炼,铁水出炉温度1400~1450℃;采用Z2140顶箱震实式造型机湿砂型造型,漏模起模,砂箱尺寸900mm×700mmx350mm;采用Z878翻台震实式制芯机,酚醛树脂砂制芯。(2)工艺分析箱体类铸件的收缩率受铁水的化学成分、浇注温度、铸件本身结构特征、铸型的退让性和型芯的退
(完整word版)变速箱壳体铸造工艺设计.doc
5.3.3变速箱壳体铸造工艺设计(1)生产条件变速箱壳体铸件材质HT200,铸件质量82kg,外形尺寸552.5mm×513mm×488.2mm,壁厚10~30mm,主要壁厚10mm,如图5.3-9。采用5t/h倒大双热风冲天炉熔炼,铁水出炉温度1400~1450℃;采用Z2140顶箱震实式造型机湿砂型造型,漏模起模,砂箱尺寸900mm×700mmx350mm;采用Z878翻台震实式制芯机,酚醛树脂砂制芯。(2)工艺分析箱体类铸件的收缩率受铁水的化学成分、浇注温度、铸件本身结构特征、铸型的退让性和型芯的退
(完整word版)变速箱壳体铸造工艺设计.doc
5.3.3变速箱壳体铸造工艺设计(1)生产条件变速箱壳体铸件材质HT200,铸件质量82kg,外形尺寸552.5mm×513mm×488.2mm,壁厚10~30mm,主要壁厚10mm,如图5.3-9。采用5t/h倒大双热风冲天炉熔炼,铁水出炉温度1400~1450℃;采用Z2140顶箱震实式造型机湿砂型造型,漏模起模,砂箱尺寸900mm×700mmx350mm;采用Z878翻台震实式制芯机,酚醛树脂砂制芯。(2)工艺分析箱体类铸件的收缩率受铁水的化学成分、浇注温度、铸件本身结构特征、铸型的退让性和型芯的退
一种超集合变速箱壳体的压铸铸造工艺.pdf
本发明公开了一种超集合变速箱壳体的压铸铸造工艺,配铝合金液;将铝合金液熔炼到700℃‑720℃,将熔炼好的铝合金液加到保温炉内,捞取表面浮渣后,将铝合金液降温至660℃‑680℃即可,准备浇注;汽车变速箱壳体铸件模具采用一模一腔分布形式,将一模一腔模具固定在2700T冷式压铸造机上,将模具预热至180℃‑200℃,然后在模具型腔内均匀喷上一层脱模剂,继续加热模具至200℃‑220℃;采用机械手料勺从吊包向挤压铸造机料桶输送铝合金液,挤压铸造机冲头向模具型腔平稳推进铝合金液、快速增压凝固结晶,充型完毕后,动
汽车变速箱壳体工艺及夹具设计.docx
毕业设计汽车变速箱壳体工艺及夹具设计学生姓名:刘犇学号:122011334系部:机械工程系专业:机械设计制造及其自动化指导教师:王玉玲二〇一六年六月诚信声明本人郑重声明:本论文及其研究工作是本人在指导教师的指导下独立完成的,在完成论文时所利用的一切资料均已在参考文献中列出。本人签名:年月日毕业设计任务书毕业设计题目:汽车变速箱壳体工艺及夹具设计系部:机械工程系专业:机械设计制造及其自动化学号:122011334学生:刘犇指导教师(含职称):王玉玲(副教授)1.课题意义及目标制造业是国家发展与社会进步的基础