
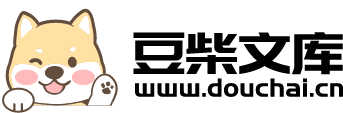
钢结构加工制作方法.docx
岚风****55
在线预览结束,喜欢就下载吧,查找使用更方便
相关资料
钢结构加工制作方法.docx
钢结构加工制作方法一、样杆、样板的制作1、样板可采用厚度0.50〜0.75mm的铁皮或塑料板制作,其精度要求见表6-2。2、样杆一般用铁皮或扁铁制作,当长度较短时可用木尺杆。样杆、样板应注明工号、图号、零件号、数量及加工边、坡部位、弯折线和弯折方向、孔径和滚圆半径等。3、样杆、样板应妥善保存,直至工程结束后方可销毁。二、号料1、核对钢材规格、材质、批号,并应清除钢板表面油污、泥土及赃物。号料方法有集中号料法、套料法、统计计算法、余料统一号料法四种。2、若表面质量满足不了质量要求,钢材应进行矫正,钢材和零件
钢结构加工制作方法.docx
钢结构加工制作方法一、样杆、样板的制作1、样板可采用厚度0.50〜0.75mm的铁皮或塑料板制作,其精度要求见表6-2。2、样杆一般用铁皮或扁铁制作,当长度较短时可用木尺杆。样杆、样板应注明工号、图号、零件号、数量及加工边、坡部位、弯折线和弯折方向、孔径和滚圆半径等。3、样杆、样板应妥善保存,直至工程结束后方可销毁。二、号料1、核对钢材规格、材质、批号,并应清除钢板表面油污、泥土及赃物。号料方法有集中号料法、套料法、统计计算法、余料统一号料法四种。2、若表面质量满足不了质量要求,钢材应进行矫正,钢材和零件
钢结构加工制作方法.docx
钢结构加工制作方法一、样杆、样板的制作1、样板可采用厚度0.50〜0.75mm的铁皮或塑料板制作,其精度要求见表6-2。2、样杆一般用铁皮或扁铁制作,当长度较短时可用木尺杆。样杆、样板应注明工号、图号、零件号、数量及加工边、坡部位、弯折线和弯折方向、孔径和滚圆半径等。3、样杆、样板应妥善保存,直至工程结束后方可销毁。二、号料1、核对钢材规格、材质、批号,并应清除钢板表面油污、泥土及赃物。号料方法有集中号料法、套料法、统计计算法、余料统一号料法四种。2、若表面质量满足不了质量要求,钢材应进行矫正,钢材和零件
第五章-钢结构工厂加工制作方法与技术措施.doc
第五章工厂加工制作方法与技术措施第一节加工重点及难点一、空心焊接球及球冠本工程钢结构空心焊接球最大截面尺寸为φ800×60,超出现行网架规范中球最大直径为φ500,加工工艺超出网架规范标准,超大超厚空心球加工是本工程钢结构加工的难点之一。墙体内外表面及屋盖上下弦表面要求平整,与杆件相连接的节点均为球冠节点,球冠直径和厚度超过现有网架规范标准,球冠加工要求高,尤其是平面部分。二、矩形钢管加工矩形钢管加工精度及变形控制难度大,矩形管与球体相贯连接节点多,矩形管相贯面无法采用机械加工,加工难度大。第二节钢结构工
钢结构墙体用挂网连接件的加工设备及其制作方法.pdf
本发明提出了钢结构墙体用挂网连接件的加工设备及其制作方法,其加工设备包括依次设置的调直送料装置、切断装置、焊接装置和放料装置;所述调直送料装置包括送料辊组和调直轮组;所述切断装置包括相对置的上断料刀和下断料台,所述焊接装置包括相对置的上焊头和下焊头,所述上断料刀和上焊头可作上下移动,当下行到位时进行断料和焊接、再上行,所述下断料台和下焊头设置在机台上,所述钢筋条经过切断装置和焊接装置时,钢筋条停止送料,所述上断料刀和上焊头下行工作,所述焊接装置将钢筋条与焊接部件焊接再由切断装置将钢筋条切断。本发明减化了加