
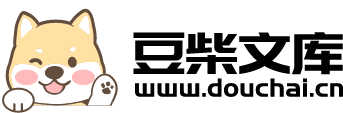
CFB炉内脱硫深度优化研究.doc
胜利****实阿
在线预览结束,喜欢就下载吧,查找使用更方便
相关资料
CFB炉内脱硫深度优化研究.doc
CFB炉内脱硫深度优化研究1、CFB炉内脱硫机理CFB锅炉通过向炉内直接添加石灰石来控制SO2排放,在流化床燃烧温度下(通常为800~900℃),投入炉内的石灰石首先在高温条件下煅烧发生分解反应生成氧化钙,然后氧化钙、SO2和氧气经过化学反应生成硫酸钙,化学反应方程式为:CaCO3→CaO+CO2CaO+SO2+1/2O2→CaSO4石灰石中的碳酸钙高温下发生分解反应,所生成的固体氧化钙再与二氧化硫及氧气反应,生成的固体硫酸钙随炉渣、飞灰一起排出炉膛从而实现固硫的目的。2、炉内脱硫反应过程SO2和O2气体
CFB炉内脱硫深度优化研究.doc
CFB炉内脱硫深度优化研究1、CFB炉内脱硫机理CFB锅炉通过向炉内直接添加石灰石来控制SO2排放,在流化床燃烧温度下(通常为800~900℃),投入炉内的石灰石首先在高温条件下煅烧发生分解反应生成氧化钙,然后氧化钙、SO2和氧气经过化学反应生成硫酸钙,化学反应方程式为:CaCO3→CaO+CO2CaO+SO2+1/2O2→CaSO4石灰石中的碳酸钙高温下发生分解反应,所生成的固体氧化钙再与二氧化硫及氧气反应,生成的固体硫酸钙随炉渣、飞灰一起排出炉膛从而实现固硫的目的。2、炉内脱硫反应过程SO2和O2气体
CFB锅炉炉内干法脱硫优化试验研究与应用.docx
CFB锅炉炉内干法脱硫优化试验研究与应用CFB锅炉炉内干法脱硫优化试验研究与应用摘要:随着环保意识不断增强,CFB锅炉炉内干法脱硫作为一种低成本、高效率、环保的脱硫方法逐渐受到重视。本文对CFB锅炉炉内干法脱硫的工作原理、优化试验研究和应用进行了分析和探讨,并结合实际案例提出了一些改进措施,为其进一步优化提供了思路。关键词:CFB锅炉;炉内干法脱硫;优化试验;改进措施一、引言CFB锅炉是一种大型的燃煤锅炉,具有低污染排放、高效节能等优点。然而,燃煤过程中会产生大量的二氧化硫等有害气体,对环境造成了不小的破
CFB炉内脱硫系统改造及自动优化控制.docx
CFB炉内脱硫系统改造及自动优化控制CFB炉内脱硫系统改造及自动优化控制摘要CFB炉内脱硫系统的改造和自动优化控制是提高锅炉运行效率、降低污染排放的关键。针对现有CFB炉内脱硫系统存在的问题,本文提出了一种改造方案,并介绍了相应的自动优化控制系统。通过实验验证,该方案可以显著提高炉内脱硫效率、降低NOx和SOx排放,同时保持燃烧效率和经济性。关键词:CFB炉;脱硫系统;改造;自动优化控制IntroductionCFB锅炉作为一种新型、高效、低污染的锅炉,已经被广泛应用。然而,脱硫系统的不完善是锅炉污染物排
CFB锅炉炉内脱硫系统存在问题及优化设计探讨.docx
CFB锅炉炉内脱硫系统存在问题及优化设计探讨摘要:CFB锅炉炉内脱硫作为一种常用的脱硫方式,在工业生产上得到了广泛的应用。但是在实际的生产中,炉内脱硫系统存在一些问题,例如蒸汽变质、炉内流态不稳定等。本文针对这些问题,通过对CFB锅炉炉内脱硫系统进行分析,并提出了优化措施及设计方案,以期能够改善炉内脱硫系统的效果,提高锅炉的整体运行效率。关键词:CFB锅炉;炉内脱硫;优化方案;设计方案一、引言CFB锅炉是近年来较为流行的一种锅炉技术,具有高热效率、低污染排放等优点,在电力、化工等领域得到了广泛的应用。其中