
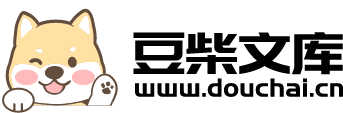
铸造工艺总汇-石膏型铸造与设计.pdf
论文****轩吖
在线预览结束,喜欢就下载吧,查找使用更方便
相关资料
铸造工艺总汇-石膏型铸造与设计.pdf
取出母模(不可敲动)起模后应立即进行点火喷烧否则易产生裂纹。(五)喷烧起模后应立刻点火并吹压缩空气进行喷烧而使陶瓷型的表面有一定的强度和硬度。(六)焙烧焙烧的目的是使陶瓷型内残存的乙醇、水分和少量的有机物烧去并使陶瓷层的强度增加。全部由陶瓷浆料灌制的陶瓷型焙烧温度可高达800oC焙烧时间2~3h出炉温度应在2500C以下以防止产生裂纹。带有水玻璃套的陶瓷型焙烧温度(烘干)在
铸造工艺总汇-石膏型铸造与设计.pdf
取出母模(不可敲动),起模后应立即进行点火喷烧,否则易产生裂纹。(五)喷烧起模后应立刻点火并吹压缩空气进行喷烧,而使陶瓷型的表面有一定的强度和硬度。(六)焙烧焙烧的目的是使陶瓷型内残存的乙醇、水分和少量的有机物烧去,并使陶瓷层的强度增加。全部由陶瓷浆料灌制的陶瓷型,焙烧温度可高达800oC,焙烧时间2~3h,出炉温度应在2500C以下,以防止产生裂纹。带有水玻璃套的陶瓷型,焙烧温度(烘干)在350~550oC。(七)浇注与清理陶瓷型浇注时定要注意挡渣。浇注温度与浇注速度可比同类型的砂型铸件稍高。陶瓷型铸件
首饰石膏型熔模铸造工艺概述.docx
首饰石膏型熔模铸造工艺概述首饰石膏型熔模铸造工艺概述随着现代工艺的不断发展,科技的不断进步,越来越多的工艺正在不断地诞生出来,而首饰石膏型熔模铸造工艺便是其中的一种。这种工艺是一种专门用来生产首饰的工艺,也是一种浇铸工艺,它的优点在于能够制造出高精度、高质量、高复杂度的首饰,而且工艺比较简单、成本较低。本文将从工艺原理、主要步骤以及优缺点三个方面进行阐述。一、工艺原理首饰石膏型熔模铸造工艺是一种以失蜡铸造为基础的工艺,它的原理非常简单,就是将首饰的模型制作出来,然后通过一系列工艺对模型进行处理,最终将其铸
石膏型熔模精密铸造工艺的研究.docx
石膏型熔模精密铸造工艺的研究石膏型熔模精密铸造工艺的研究摘要:石膏型熔模精密铸造是一种新兴的精密铸造工艺,具有高精度、高表面质量和高加工效率的特点。本论文通过对石膏型熔模精密铸造工艺的研究,分析了工艺的基本原理和关键技术,探讨了工艺的优化方法,以提高石膏型熔模精密铸造的质量和效率。关键词:石膏型熔模,精密铸造,工艺研究,优化方法1.引言随着科学技术的发展,对于精密铸造工艺的要求也越来越高。而石膏型熔模精密铸造作为一种新型的工艺,具有诸多优势,在航空航天、汽车制造等领域得到广泛应用。本论文旨在通过对石膏型熔
精密铸造用石膏型体快速焙烧工艺.pdf
本发明公开一种精密铸造用石膏型体快速焙烧工艺,该石膏型体快速焙烧工艺包括首先将石膏混合料浆料浇注在铁制型壳内,该石膏型体快速焙烧工艺还包括以下步骤:(1)将带铁质型壳的石膏型放到工业微波炉中干燥20~60分钟,出炉进入下一工序;(2)将步骤(1)工序的产品放入电炉中进行焙烧,升温的最高温度为700~800℃,再保温1~2小时后,随炉冷却至适合浇注的温度;本发明技术方案采用的快速焙烧工艺的时间缩短了16~34h,节约了大量的电能。