
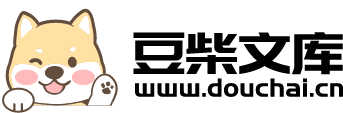
FMEA教材.ppt
依波****bc
亲,该文档总共144页,到这已经超出免费预览范围,如果喜欢就直接下载吧~
相关资料
FMEA教材.ppt
潜在失效模式及后果分析FMEA课程大纲一、产品风险与可靠度一、产品风险与可靠度一、产品风险与可靠度一、产品风险与可靠度二、FMEA的基本概念二、FMEA的基本概念二、FMEA的基本概念二、FMEA的基本概念二、FMEA的基本概念二、FMEA的基本概念二、FMEA的基本概念二、FMEA的基本概念二、FMEA的基本概念二、FMEA的基本概念二、FMEA的基本概念二、FMEA的基本概念二、FMEA的基本概念二、FMEA的基本概念二、FMEA的基本概念二、FMEA的基本概念二、FMEA的基本概念二、FMEA
FMEA 教材.ppt
FMEA课程目的FMEA为什么是小组经验的集成?什么是FMEA?失效的定义FMEA的失效模式FMEA的起源FMEA的起源典型的FMEAsFMEAs的关联FMEA的时间顺序FMEA的关键术语汽车行业缩略语过程流程图典型的开发三部曲控制计划/过程流程结合图例FMEA的益处FMEA的前提条件FMEA小组成功的FMEA小组FMEA小组的守则FMEA小组的守则FMEA小组会议的责任FMEA小组决定的标准/模式脑力风暴Brainstorming脑力风暴Brainstorming脑力风暴Brainstorming设计F
FMEA 教材.ppt
對FMEA的認知一、產品風險與可靠度一、產品風險與可靠度一、產品風險與可靠度二、FMEA的基本概念二、FMEA的基本概念二、FMEA的基本概念二、FMEA的基本概念二、FMEA的基本概念二、FMEA的基本概念二、FMEA的基本概念FMEA之演變國際間採用FMEA之狀況二、FMEA的基本概念二、FMEA的基本概念FMEA之功用FMEA之特徵QS9000設計/製程FMEA表腦力激盪法MLD-STD-1629AFMECA(三、設計FMEA填寫說明)(三、設計FMEA填寫說明)(三、設計FMEA填寫說
FMEA教材(正式教材).ppt
FMEA原理及运用课堂纪律扁鹊三兄弟故事扁鹊大哥擅长的是“事前预防”,具有敏锐的洞察力和战略眼光,能够帮助人们防患于未然。因此,如果在现代社会,扁鹊大哥应该比较适合去卖保险或者保健品——赶快保健,重视保健,一句“君有疾在腠理,不治将恐深”已足以让现代人提心吊胆。而且,这年头,如果保险或者保健品卖得好,更容易出名。当然,如果扁鹊大哥不想去卖保险或者保健品,也可以到企业去做战略规划、项目投资的特聘专家。总之,一句话,在这个一切成功的要素都已经存在的今天,战略眼光已经显得比能力更加重要。扁鹊二哥擅长的是“事中控
FMEA教材(正式教材).ppt
FMEA原理及运用课堂纪律扁鹊三兄弟故事扁鹊大哥擅长的是“事前预防”具有敏锐的洞察力和战略眼光能够帮助人们防患于未然。因此如果在现代社会扁鹊大哥应该比较适合去卖保险或者保健品——赶快保健重视保健一句“君有疾在腠理不治将恐深”已足以让现代人提心吊胆。而且这年头如果保险或者保健品卖得好更容易出名。当然如果扁鹊大哥不想去卖保险或者保健品也可以到企业去做战略规划、项目投资的特聘专家。总之一句话在这个一切成功的要素都已经存在的今天战略眼光已经显得比能力更加重要。扁鹊二哥擅长的是“事中