
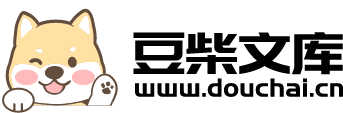
炼钢工序节能减排技术研究与应用.docx
mm****酱吖
在线预览结束,喜欢就下载吧,查找使用更方便
相关资料
炼钢工序节能减排技术研究与应用.docx
炼钢工序节能减排技术研究与应用摘要:主要介绍了转炉炼钢的优势转炉负能炼钢技术和转炉煤气干法净化回收技术的原理、工艺、节能效果、应用情况及发展前景并提出钢铁行业节能减排的发展方向。关键词:转炉冶炼;负能炼钢;节能减排;干法净化;湿法净化0引言目前中国钢铁行业各个工序的能耗与发达国家相比差距很大特别是在转炉冶炼环节发达国家为负能耗而国内转炉环节产生的煤气和蒸汽利用率非常低能耗较高且部分转炉没有回收装置转炉煤气热值非常高是高炉煤气热值的1倍多不仅造成了
炼钢工序节能减排技术研究与应用.docx
炼钢工序节能减排技术研究与应用摘要:主要介绍了转炉炼钢的优势转炉负能炼钢技术和转炉煤气干法净化回收技术的原理、工艺、节能效果、应用情况及发展前景并提出钢铁行业节能减排的发展方向。关键词:转炉冶炼;负能炼钢;节能减排;干法净化;湿法净化0引言目前中国钢铁行业各个工序的能耗与发达国家相比差距很大特别是在转炉冶炼环节发达国家为负能耗而国内转炉环节产生的煤气和蒸汽利用率非常低能耗较高且部分转炉没有回收装置转炉煤气热值非常高是高炉煤气热值的1倍多不仅造成了
烧结工序节能减排技术研究综述.docx
烧结工序节能减排技术研究综述烧结工序是冶金、矿业、化工等行业中重要的生产工序之一,其作用是将粉状原料在高温下烧结成固体块状物体。然而,烧结工序产生的能耗和排放问题成为当前亟待解决的环境问题。为了实现工业生产的可持续发展,研究人员开展了大量的节能减排技术研究。本文综述了目前在烧结工序中应用的节能减排技术,并分析了其优缺点和发展前景。一、烧结工序的能耗和排放状况烧结工序是一个能耗较高的工序,其耗电量主要集中在烧结机、风机和热交换设备等设备上。此外,燃料的燃烧也会产生大量的二氧化碳等废气排放。因此,研究如何降低
节能减排措施在乙炔工序中的应用.docx
节能减排措施在乙炔工序中的应用随着人们对环境保护意识的增强,越来越多的企业开始关注自身的生产过程对环境的影响。乙炔生产作为化学行业重要的一环,对环境有着不小的影响。因此,应通过实施节能和减排措施来减少环境影响,提高工艺水平,增强企业的可持续发展能力。一、乙炔生产流程及环境污染乙炔是一种重要的石油化工原料,在化学行业中有着广泛的应用。乙炔生产的主要原料是炭黑和石灰石,其生产流程如下:炭黑和石灰石经过炉子预热,进入电解炉中。在电解炉中,经过电解,产生氢气和乙炔。电解过程中,还会产生一些副产物,如一氧化碳、二氧
装卸机械节能减排创新技术研究与应用.pdf
万方数据装卸机械节能减排创新技术研究与应用上海国际港务(集团)股份有限公司包起帆RTG油改电国民经济快速增长与资源瓶颈矛盾日益突出。上海港重点围绕以下几个方面开展了节能降耗的新技术研究与实践。轮胎式集装箱门式起重机(RTG)依赖起重机自身配置的柴油发电机组所提供的电源进行工作,“喝油”厉害,能量转换效率低,能耗大,且柴油价格电网供电高3倍,而且柴油机气体排放、噪声、废油水泄漏,均对环境形成较大的污染。油改电RTG势在必行。根据各港区堆场的特点,我们采用磁滞联其原理都是在原有的一组柴油机发电机组发电的情况下