
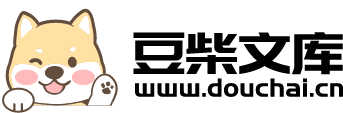
浅谈薄壁零件的加工方法.docx
猫巷****志敏
在线预览结束,喜欢就下载吧,查找使用更方便
相关资料
浅谈薄壁零件的加工方法.docx
浅谈薄壁零件的加工方法摘要:模具制造经常会遇到使用数控铣或加工中心加工薄壁零件(铜合金的电极)针对薄壁类刚性差、加工工艺性差、易发生加工变形和切削振动等情况本文通过改进薄壁零件加工方法和切削工艺合理地选择刀具优化编程等策略来保证薄壁零件加工后的变形和精度达到要求。关键词:薄壁工件加工变形加工方法一、前言如下图1此类薄壁电极零件在模具制造过程中很常见如数码类、手机类、机壳类等产品模具的加工尤为重要薄壁电极在模具行业也称骨位。电极材料通常使用铜
浅谈薄壁零件的加工方法.docx
浅谈薄壁零件的加工方法摘要:模具制造经常会遇到使用数控铣或加工中心加工薄壁零件(铜合金的电极)针对薄壁类刚性差、加工工艺性差、易发生加工变形和切削振动等情况本文通过改进薄壁零件加工方法和切削工艺合理地选择刀具优化编程等策略来保证薄壁零件加工后的变形和精度达到要求。关键词:薄壁工件加工变形加工方法一、前言如下图1此类薄壁电极零件在模具制造过程中很常见如数码类、手机类、机壳类等产品模具的加工尤为重要薄壁电极在模具行业也称骨位。电极材料通常使用铜
浅谈提高薄壁零件加工精度的工艺方法.docx
浅谈提高薄壁零件加工精度的工艺方法提高薄壁零件加工精度对于制造业来说至关重要。薄壁零件广泛应用于汽车、电子设备、航空航天等领域,要求其加工精度高、尺寸稳定、表面质量好。本文将从工艺方法的角度,浅谈如何提高薄壁零件加工精度。首先,选择合适的材料是提高薄壁零件加工精度的关键。材料的稳定性和机械性能直接影响加工精度。通常情况下,选择具有较高强度和较好可塑性的材料作为薄壁零件的加工材料,如铝合金、不锈钢等。这些材料具有较高的硬度和强度,可以降低加工变形和形状失真的风险,从而提高加工精度。其次,选择适当的加工方法也
薄壁零件的加工方法.pdf
本发明公开了一种薄壁零件的加工方法,包括余量预留,沿着零件直径最大外圆处预留一条与零件同轴的环形加工余量边;凹槽加工,在所述环形加工余量边上加工一条与零件同轴的环形凹槽;零件装夹,以环形加工余量边上垂直于零件轴线方向的端面为支撑边,以环形加工余量边的外周向面为定位面,以环形凹槽内垂直于零件轴线方向的环形面为压钩压紧面。本发明避免了同一零件加工时应用多个夹具,减少了夹具组合带来的时间和生产成本,采用支撑定位压紧方式防止零件变形,零件压钩隐藏在零件内部,对深度方向的车削及测量不造成干涉。
薄壁零件的加工方法.pdf
本发明薄壁零件的加工方法涉及机械加工领域,具体涉及薄壁零件的加工方法,包括以下步骤:粗加工,薄壁部位与其他部位一起粗加工,薄壁部位宽处要留1mm加工余量防止粗加工时因速度快、吃刀量大造成薄壁部位变形,粗加工方式应采用环绕走刀式,一次走刀由四周向中间螺旋扩展至侧壁;较为有效的降低了刀具接近薄壁部位时产生撞击力造成薄壁部位变形,同时刀具要求有足够的强度,刀具选择钨钢刀立铣刀。半精加工顶曲面,选择6mm球刀,曲面半精加工,去除过多的残料,使精加工余量均匀;本发明操作简单,方便操作,且能保证工件的加工质量和加工精