
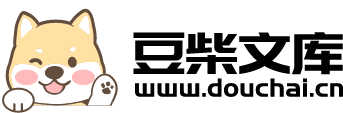
浅谈磨削裂纹的产生与防止.docx
建英****66
在线预览结束,喜欢就下载吧,查找使用更方便
相关资料
浅谈磨削裂纹的产生与防止.docx
浅谈磨削裂纹的产生与防止【摘要】淬火件尤其是渗碳淬火件磨削时常常出现磨削裂纹它不但影响外观还直接影响工件的质量。通过长期的尝试与总结本文将对磨削裂纹的产生及防止作出阐述并对已出现的磨削裂纹提出行之有效的消除方法。【关键词】淬火;磨削裂纹;预防措施1.引言磨削裂纹的形状很独特一眼就可以看出它与一般的淬火裂纹有明显不同较轻的磨削裂纹呈垂直于磨削方向的平行线称之为第一类裂纹。较严重的磨削裂纹呈龟甲状又叫龟裂或者第二类裂纹其深度大致为0.05~0.2m
浅谈磨削裂纹的产生与防止.docx
浅谈磨削裂纹的产生与防止【摘要】淬火件尤其是渗碳淬火件磨削时常常出现磨削裂纹它不但影响外观还直接影响工件的质量。通过长期的尝试与总结本文将对磨削裂纹的产生及防止作出阐述并对已出现的磨削裂纹提出行之有效的消除方法。【关键词】淬火;磨削裂纹;预防措施1.引言磨削裂纹的形状很独特一眼就可以看出它与一般的淬火裂纹有明显不同较轻的磨削裂纹呈垂直于磨削方向的平行线称之为第一类裂纹。较严重的磨削裂纹呈龟甲状又叫龟裂或者第二类裂纹其深度大致为0.05~0.2m
磨削裂纹产生的原因及其防止方法.docx
磨削裂纹产生的原因及其防止方法磨削裂纹可能是一些重要机器部件因为错误或不充分的维护而导致的机械衰退和失效。磨削是常见的材料处理过程,其中磨削面的质量和平滑度是关键因素。在磨削过程中,裂纹经常会出现在材料表面或材料内部。本文将探讨磨削裂纹的产生原因以及如何预防它们。磨削裂纹的产生原因主要分为四类:材料选择、磨削工艺,磨削剂和过热。对于每个类别,它们在磨削过程中产生裂纹的原因如下:1.材料选择材料的物理和化学性质决定了其磨削能力。如果我们选择的材料太脆,则在磨削时,它很可能会因过度颤动而破碎。相反,如果我们选
防止磨削裂纹的操作方法.docx
防止磨削裂纹的操作方法防止磨削裂纹的操作方法磨削裂纹是磨削加工中常见的磨损形式,造成零部件的失效和损坏,严重影响设备的可靠性和寿命。因此,如何防止磨削裂纹的产生成为磨削加工中亟需解决的问题。1.选择合适的磨削工件材料磨削裂纹的产生与材料的断裂韧性和磨削过程中的应力分布有关,因此选择具有高断裂韧性的材料可以提高防止磨削裂纹的能力。比如高速钢、金属陶瓷等材料在磨削加工中表现出较好的抗裂纹能力。2.精细的磨削工艺参数控制磨削过程中的切屑形态和切削力的大小会影响应力的分布,从而影响磨削裂纹的产生。因此,在磨削加工
防止通心粉产生裂纹的研究.docx
防止通心粉产生裂纹的研究防止通心粉产生裂纹的研究引言:通心粉是一种受欢迎的粉状食品,具有方便快捷、易于携带等特点。然而,通心粉的制作过程中容易出现裂纹现象,导致产品质量下降。为了解决这个问题,本研究将从原料选择、加工技术以及储存条件等方面进行探讨,以期为通心粉的生产提供技术支持。一、原料选择1.选择优质小麦粉:通心粉的主要原料是面粉,因此选择优质小麦粉是防止通心粉产生裂纹的关键。优质小麦粉有较高的蛋白质含量和弹性,能够提高通心粉的黏合性,并且能够提供更好的韧性。2.加入适量的淀粉:淀粉是通心粉制作过程中添