
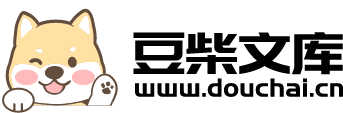
耐热钢涡壳真空吸铸工艺的反重力补缩壳型结构.pdf
运升****魔王
在线预览结束,喜欢就下载吧,查找使用更方便
相关资料
耐热钢涡壳真空吸铸工艺的反重力补缩壳型结构.pdf
本发明公开了一种耐热钢涡壳真空吸铸工艺的反重力补缩壳型结构,涉及特种铸造技术领域,该结构通过由周围壳型向中心的向上倾斜的内吸口及直吸道的负压作用,可在无冒口的条件下通过钢液的反重力作用对铸件进行补缩,提高补缩效率,有效解决铸件内部缩孔缩松缺陷,防止铸件内漏,保证铸件质量。此结构设计保证了钢液的上升回落,使得充型阶段钢液能够顺利上升,凝固保压阶段钢液强化补缩,及泄压阶段直吸道内钢液迅速回落。该结构设计按照铸件、内吸口、直吸道的顺序凝固原则,强化了铸件的补缩能力。在铸件凝固补缩结束后泄压,直吸道内钢液回流,仅
一种耐热钢涡壳真空吸铸工艺的反重力补缩壳型结构.pdf
本发明公开了一种耐热钢涡壳真空吸铸工艺的反重力补缩壳型结构,涉及特种铸造设备领域,该结构通过向上倾斜的内吸口及直吸道的负压作用,可在无冒口的前提下通过钢液的反重力作用对铸件进行补缩,提高补缩效率,有效解决铸件内部缩孔缩松缺陷,防止铸件内漏,保证铸件质量。此结构设计保证了钢液的上升回落,使得充型阶段钢液能够顺利上升,凝固保压阶段钢液强化补缩,及泄压阶段直吸道内钢液迅速回落。该结构设计按照铸件、内吸口、直吸道的顺序凝固原则,强化了铸件的补缩能力。在铸件凝固补缩结束后泄压,直吸道内钢液回流,仅留很小的内吸口补缩
一种驱动桥壳补缩工艺.pdf
本发明涉及车桥制造业,一种驱动桥壳补缩工艺在利用铁水进行浇灌补缩时,在桥壳上只开设一个高热冒口。高发热冒口采用金属易割片,敲落冒口在铸件表面残留小,降低了清理打磨工作量,提高了铁水利用率、工艺出品率,节约了生产成本。?
铝合金涡壳金属型重力铸造工艺设计及优化.docx
铝合金涡壳金属型重力铸造工艺设计及优化随着科技的不断发展,铝合金材料越来越被广泛应用于各种领域。其中,涡壳金属型重力铸造技术已经成为铝合金铸造中的一种重要工艺。本文将从涡壳金属型重力铸造工艺的设计、优化等方面进行探讨。一、工艺设计1、涡壳设计涡壳是涡壳金属型铸造过程中的关键部件,涡壳的设计直接影响到铸造件的质量。涡壳的设计应满足以下要求:(1)外形合理,容易制造,并能够保证较高的细晶度和灵活性。(2)降低列管出现的可能性,减少冷却时间。(3)顶棒与涡壳之间的距离应在10mm-20mm之间,以便于涡壳的回填
一种反重力真空吸铸耐热铸钢铸造工艺及装置.pdf
本发明公开了一种反重力真空吸铸耐热铸钢铸造工艺及装置。主要通过在砂型型腔设置真空后,是对型腔与大气建立压差,使得钢液进入砂型完成铸件充型的过程;然后对钢水要快速截流并释放真空,使得直浇道剩余钢液通过重力作用回炉,达到节省节约金属液的作用。通过使用真空吸铸的方法改变铸件充型的时间,可以减小铸件过冷现象,制作薄壁铸件;可以降低充型的温度减小能耗,充型温度低同时减小铸件的缩松倾向;充型时砂型形成真空对于铸件产生气孔可以避免;通过工艺装置在实现铸件充型完成后,加快平浇道凝固后释放直浇道金属液的方法提高铸件出品率,