
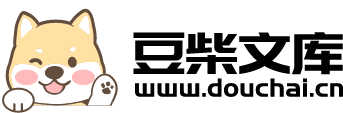
大型锥孔加工工艺论文.docx
康佳****文库
在线预览结束,喜欢就下载吧,查找使用更方便
相关资料
大型锥孔加工工艺论文.docx
大型锥孔加工工艺论文1大型薄壁锥孔测量工具的必要性及加工工艺的简介对于大型薄壁锥孔测量工具加工工艺的主要内容包括很多首先主要是该大型锥孔测量装置是GM200-180辊压磨产品中辊套锥孔工装辊套活件比较大内锥孔大端直径φ1400-1.5-1.56mm孔的锥度1:30孔深1800mm而且精度要求高。如此大内孔锥度及孔深是前所未有不仅测量方法及测量工具难以实现更主要是测量工具的加工也存在较大困难。传统的锥度测量方法和手段已满足不了要求针对这类大型活件采用独特的测量方法通过
大型锥孔加工工艺论文.docx
大型锥孔加工工艺论文1大型薄壁锥孔测量工具的必要性及加工工艺的简介对于大型薄壁锥孔测量工具加工工艺的主要内容包括很多首先主要是该大型锥孔测量装置是GM200-180辊压磨产品中辊套锥孔工装辊套活件比较大内锥孔大端直径φ1400-1.5-1.56mm孔的锥度1:30孔深1800mm而且精度要求高。如此大内孔锥度及孔深是前所未有不仅测量方法及测量工具难以实现更主要是测量工具的加工也存在较大困难。传统的锥度测量方法和手段已满足不了要求针对这类大型活件采用独特的测量方法通过
锥孔加工工具及锥孔加工方法.pdf
本发明公开一种锥孔加工工具及锥孔加工方法,其中,锥孔加工工具包括:刀具主体;装配套,装配套与刀具主体可拆连接,装配套的内周壁凹设有沿其轴向延伸的三个以上的装配槽,三个以上的装配槽沿着装配套的周向均匀排布,三个以上的装配槽的槽底均呈圆弧状设置,三个以上的装配槽的槽底均朝同一方向倾斜设置;装配槽的槽底部分贯穿,形成沿其长度方向延伸的让位开口;若干挤压圆柱棒分设于对应的装配槽内,挤压圆柱棒的一侧与对应的装配槽的槽底配合并自对应的让位开口伸出,挤压圆柱棒的另一侧与装配槽的槽口相齐平;刀具主体与装配套插接配合,以使
利用锥孔刀具加工锥孔的方法.pdf
本发明涉及机械加工技术领域,尤其涉及一种利用锥孔刀具加工锥孔的方法,使用特制的锥孔刀具,在锥孔刀具的前端设置有刀杆,该刀杆的侧面上沿圆锥螺旋线设置有若干个铣刀,相邻铣刀沿轴向方向的间距为4~8mm,相邻铣刀之间的夹角为不大于120°,在工件表面钻基准孔,使用所述锥孔刀具沿基准孔按转速不低于600转/分、进给量不低于1.0mm/转进行加工形成多级台阶孔,控制锥孔刀具的深度使得单边预留0.25mm,然后使用镗刀或绞刀将多级台阶孔加工成锥孔,分布的多个铣刀可以加工小台阶的多台阶孔,并且加工时,转速和进给量比现有
尼龙液压接头锥孔的高效加工工艺.pdf
第卷年月工程机械MaterialsandProcesses材