
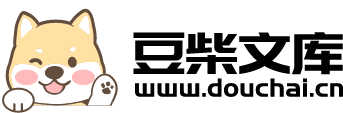
高强钢大直径内螺纹超声滚压强化技术.docx
快乐****蜜蜂
在线预览结束,喜欢就下载吧,查找使用更方便
相关资料
高强钢大直径内螺纹超声滚压强化技术.docx
高强钢大直径内螺纹超声滚压强化技术高强钢大直径内螺纹超声滚压强化技术摘要高强钢大直径内螺纹件在工程领域中具有广泛的应用,但其在使用过程中容易出现断裂和疲劳等问题。为解决这些问题,需要对这类件进行强化处理。超声滚压强化技术是一种有效的方法,可以提高材料的抗疲劳性能和强度。本论文详细介绍了高强钢大直径内螺纹超声滚压强化技术的原理和应用,分析了其对材料性能的影响,并总结了该技术存在的问题和发展趋势。关键词:高强钢、大直径内螺纹、超声滚压强化、抗疲劳性能、强度1.引言高强钢大直径内螺纹件是一种常见的工程结构件,被
高强度钢内螺纹冷挤压成形技术.docx
高强度钢内螺纹冷挤压成形技术高强度钢内螺纹冷挤压成形技术摘要:随着工程技术的发展,对于高强度钢的需求越来越大。高强度钢在航空、汽车、舰船等领域有着广泛的应用。而内螺纹冷挤压成形技术是一种常用的加工方法,可以提高高强度钢的综合性能。本文首先介绍了高强度钢的概念和分类,接着阐述了内螺纹冷挤压成形技术的原理和方法,并分析了其在高强度钢加工中的应用和优势。最后,针对内螺纹冷挤压成形技术存在的问题和发展趋势进行了探讨。关键词:高强度钢、内螺纹、冷挤压成形、综合性能1.引言随着现代工程技术的进步,人们对于材料的要求越
超声滚压技术在表面强化中的研究与应用进展.docx
超声滚压技术在表面强化中的研究与应用进展随着工业化程度的不断提高,人们对材料性能的需求也在不断增加。而表面强化技术作为一种提升材料性能的有效手段,受到了越来越广泛的关注。超声滚压技术作为一种新兴的表面强化技术,其独特的滚压方法和超声波的作用,使其在材料表面强化领域引起了极大的兴趣。本文将对超声滚压技术在表面强化中的研究与应用进展进行综述。一、超声滚压技术概述超声滚压技术是一种结合了超声振动和滚压技术的新型表面强化技术。该技术通过超声波的作用,使滚轮表面发生微小振动,从而增强了滚压过程中的弹塑性变形,改善了
一种MJ内螺纹滚压强化方法.pdf
本发明公开了一种MJ内螺纹滚压强化方法,其主要包括以下步骤:1)、按所述MJ内螺纹要求在零件上加工内螺纹;2)、选用与所述内螺纹相匹配的滚轮,安装零件及滚轮于机床上,调节滚轮中心与零件待滚压内螺纹中心一致;3)、设置机床参数,使滚压沿轴向的进给与零件转速匹配;4)、对刀,记下滚轮轮缘与螺纹根部相接触时的径向初始位置,将滚轮退到外螺纹之外;5)、启动机床,当滚轮进入内螺纹半个螺距时,调节中托板使滚轮径向达到规定的滚压量,滚压到螺纹退刀槽,停止机床并退出滚轮,卸下零件。本发明的MJ内螺纹滚压强化方法工艺简单、
超声滚压强化的工艺试验.docx
超声滚压强化的工艺试验超声滚压强化是一种金属表面处理技术,通过利用超声波能量和滚压力对材料进行变形,从而改善材料的力学性能和表面质量。本文将对超声滚压强化的工艺试验进行介绍和分析。一、超声滚压强化的原理和机制超声滚压强化技术是将超声波振动与滚压力结合起来应用于金属的表面处理。超声波振动可以引起材料的微小位移和应力,从而对材料进行变形和压实。滚压力则通过对材料施加外力,使其发生塑性变形,从而改变材料的晶粒结构和力学性能。在超声滚压强化过程中,超声波振动的主要作用是引起材料表层的微观位移和应力。这些微观变形使