
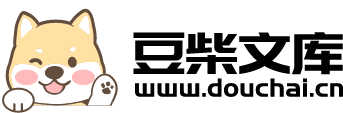
基于铸造毛坯的大型水轮机叶片多轴联动数控加工方法.pdf
景福****90
在线预览结束,喜欢就下载吧,查找使用更方便
相关资料
基于铸造毛坯的大型水轮机叶片多轴联动数控加工方法.pdf
本发明公开了一种基于铸造毛坯的大型水轮机叶片多轴联动数控加工方法,所述方法步骤包括:1)采用大型三坐标检测机对水轮机叶片毛坯进行三维坐标检测,运用扫描仪对叶片毛坯进行点云采集;2)根据步骤1)中得到的叶片毛坯三维坐标数据和点云数据,计算机对叶片毛坯的三维坐标数据和点云数据处理后生成叶片实体毛坯的计算机模型;3)基于步骤2)得到的叶片实体毛坯的计算机模型对巨型水轮机叶片的毛坯实体通过数控编程进行加工,规划刀位轨迹,并进行机床模拟切削仿真。本发明方法可得到准确的叶片毛坯实体计算机模型,对毛坯实体可进行灵活的预
大型混流式叶片的多轴联动数控加工编程技术.pdf
大型混流式叶片的多轴联动数控加工编程技术一、引言水轮机是水力发电的原动机,水轮机转轮叶片的制造转轮的优劣对水电站机组的安全、可靠性、经济性运行有着巨大的影响。水轮机转轮叶片是非常复杂的雕塑面体。在大中型机组制造工艺上,长期以来采用的“砂型铸造→砂轮铲磨→立体样板检测”的制造工艺,不能有效地保证叶片型面的准确性和制造质量。目前采用五轴联动数控加工技术是当今机械加工中的尖端高技术。大型复杂曲面零件的数控加工编程则是实现其数字化制造的最重要的技术基础,其数控编程技术是一个数字化仿真评价及优化过程。其关键技术包括
多叶片转轮曲面的三轴联动加工方法.pdf
本发明涉及一种多叶片转轮曲面的三轴联动加工方法。其加工工艺步骤为:以工件回转中心为零点、以其中一片叶轮筋线为Z轴建立工件坐标系;根据叶片数将工件分为a个工位;设工位n对应的叶轮筋线为叶片n,叶片n+1与工位n主轴夹角为ɑ;将每片叶片的内部曲面按背部投影曲线分割成m块各自相连的曲面区域,依次命名;对各叶片内、背部曲面区域在各工位下编程模拟生成各工位下的加工程序;将工件安装于回转工作台上;回转工作台按叶片内、背部曲面区域1~m对应的工位转动,逐一完成所有叶片内部与背部曲面的加工。本发明的优点是,使用具有回转工
一种大型水轮机叶片的铸造方法.pdf
本发明涉及一种水轮机叶片的立体组芯铸造方法,尤其是涉及一种大型水轮机叶片的铸造方法,其特征是:它包括如下步骤:工艺设计、制作芯盒、制作芯骨、制芯、修补砂芯、组芯、放进砂箱,铺设直浇道,砂芯周围用硅砂围住、合箱、压箱、浇注、冒口切割、热处理、型线检测、铲磨和抛丸;本发明提供一种能显著缩短生产周期、降低生产叶片的设备能力要求、操作简便、易于控制,实现叶片批量化生产。
基于NX(UnigraphicsNX)的叶片零件多轴数控加工研究.docx
基于NX(UnigraphicsNX)的叶片零件多轴数控加工研究基于NX(UnigraphicsNX)的叶片零件多轴数控加工研究摘要:随着工业技术的不断发展,多轴数控加工技术在制造业中得到了广泛的应用。本文以叶片零件的多轴数控加工为研究对象,通过分析叶片零件的特点和多轴数控加工的原理,在NX软件平台上进行了叶片零件的多轴数控加工仿真实验,并对结果进行了分析和总结,为叶片零件的多轴数控加工提供了参考。关键词:叶片零件;多轴数控加工;NX软件1.引言叶片零件是一种在航空航天、能源等领域广泛应用的重要零件。而多