
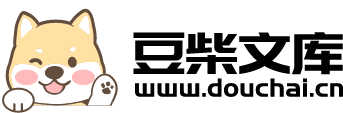
大型混流式叶片的多轴联动数控加工编程技术.pdf
qw****27
在线预览结束,喜欢就下载吧,查找使用更方便
相关资料
大型混流式叶片的多轴联动数控加工编程技术.pdf
大型混流式叶片的多轴联动数控加工编程技术一、引言水轮机是水力发电的原动机,水轮机转轮叶片的制造转轮的优劣对水电站机组的安全、可靠性、经济性运行有着巨大的影响。水轮机转轮叶片是非常复杂的雕塑面体。在大中型机组制造工艺上,长期以来采用的“砂型铸造→砂轮铲磨→立体样板检测”的制造工艺,不能有效地保证叶片型面的准确性和制造质量。目前采用五轴联动数控加工技术是当今机械加工中的尖端高技术。大型复杂曲面零件的数控加工编程则是实现其数字化制造的最重要的技术基础,其数控编程技术是一个数字化仿真评价及优化过程。其关键技术包括
基于铸造毛坯的大型水轮机叶片多轴联动数控加工方法.pdf
本发明公开了一种基于铸造毛坯的大型水轮机叶片多轴联动数控加工方法,所述方法步骤包括:1)采用大型三坐标检测机对水轮机叶片毛坯进行三维坐标检测,运用扫描仪对叶片毛坯进行点云采集;2)根据步骤1)中得到的叶片毛坯三维坐标数据和点云数据,计算机对叶片毛坯的三维坐标数据和点云数据处理后生成叶片实体毛坯的计算机模型;3)基于步骤2)得到的叶片实体毛坯的计算机模型对巨型水轮机叶片的毛坯实体通过数控编程进行加工,规划刀位轨迹,并进行机床模拟切削仿真。本发明方法可得到准确的叶片毛坯实体计算机模型,对毛坯实体可进行灵活的预
混流式叶片的数控加工技术.docx
混流式叶片的数控加工技术引言:混流式叶片是航空发动机、燃气轮机、水力涡轮机等领域中使用的一种重要部件。为了有效提升叶片的性能,现代的制造技术多采用数控加工技术。在本文中,我们将重点研究混流式叶片数控加工技术相关内容,包括:数控编程、数控机床加工、质量控制等方面。一、混流式叶片数控编程混流式叶片的数控编程可以通过数学模型和计算机软件实现。绘制叶片的三维模型,根据叶片的形状、尺寸、转速、叶根、叶尖等参数,利用数学分析方法获得混流式叶片在剖面、轴向、弯曲方向上的形状数据,将其转化为可执行的G代码,以指导数控机床
多轴、多通道数控加工编程技术研究.docx
多轴、多通道数控加工编程技术研究一、引言随着科技的不断发展,数控加工技术在制造业中得到了广泛的应用。对于传统的数控加工技术,其只能进行比较简单的加工操作,受到制约较大。而在多轴、多通道数控加工编程技术的推动下,大大提高了加工效率和加工精度,为制造业的发展提供了巨大的帮助。本文将从多轴、多通道数控加工编程技术的概念、发展历程、关键技术及应用现状等方面进行探讨,希望能够对读者有所启发。二、多轴、多通道数控加工编程技术的概念多轴、多通道数控加工编程技术是指利用一定的编程方式,使数控加工机床能够同时控制多个轴线进
混流式转轮铸造叶片的数控加工难点及解决方法.docx
混流式转轮铸造叶片的数控加工难点及解决方法一、绪论混流式转轮铸造叶片广泛应用于航空、航天、能源等重要领域。由于其复杂的形状和高精度要求,混流式转轮铸造叶片的数控加工需要克服一些难点。本文将对混流式转轮铸造叶片的数控加工难点及解决方法展开讨论。二、混流式转轮铸造叶片的数控加工难点2.1叶片形状复杂混流式转轮铸造叶片作为航空、航天、能源等领域的重要部件,其形状设计十分复杂,存在大量的曲面和变化。2.2数量庞大混流式转轮铸造叶片数目众多,批量生产,但是每个叶片都需要高精度的加工,所以生产效率是一个挑战。2.3具