
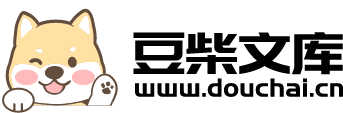
CNC机床伺服系统跟随误差与轮廓误差分析.docx
快乐****蜜蜂
在线预览结束,喜欢就下载吧,查找使用更方便
相关资料
CNC机床伺服系统跟随误差与轮廓误差分析.docx
CNC机床伺服系统跟随误差与轮廓误差分析CNC机床的伺服系统是数控加工领域的重要部分。其作用是控制运动轴的位置和速度,保证机床加工精度和稳定性。伺服系统的跟随误差和轮廓误差是影响CNC机床加工精度的两个主要因素,本文将对它们的原因和解决方法进行分析。一、伺服系统跟随误差伺服系统跟随误差是指CNC机床在切削过程中运动轴跟随设定轨迹时产生的误差。这种误差主要来自机床伺服系统的控制精度和动态响应能力。控制精度方面,伺服系统的位置误差常常受到控制器输出精度、数字-模拟转换器的精度和机床电气系统稳定性的影响。在数字
CNC机床动态特性与S形试件轮廓误差映射关系分析.docx
CNC机床动态特性与S形试件轮廓误差映射关系分析摘要本文研究了CNC机床动态特性与S形试件轮廓误差映射关系。首先介绍了CNC机床的基本概念和组成结构,重点分析了CNC机床动态特性,包括加工误差、稳定性和响应速度等方面。然后,介绍了S形试件的定义和特点,分析了S形试件加工过程中出现的轮廓误差以及其产生的原因。接着,利用实验数据对CNC机床动态特性与S形试件轮廓误差映射关系进行了分析,发现CNC机床动态特性与S形试件轮廓误差之间存在一定的相关性。最后,提出了针对CNC机床动态特性与S形试件轮廓误差映射关系的优
CNC多轴联动的机床交叉耦合轮廓误差补偿技术.pptx
汇报人:CONTENTS添加章节标题CNC多轴联动机床的基本原理其基本原理是通过计算机控制,实现多个轴的同步运动,从而完成复杂的加工任务。***C多轴联动机床可以大大提高加工效率和精度,广泛应用于航空航天、汽车制造等领域。***C多轴联动机床的发展趋势是智能化、高精度和高效率。***C多轴联动机床可以大大提高加工效率和精度,广泛应用于航空航天、汽车制造等领域。***C多轴联动机床的发展趋势是智能化、高精度和高效率。CNC多轴联动机床的工作原理CNC多轴联动机床的应用领域交叉耦合轮廓误差的产生原因几何误差热
CNC多轴联动的机床交叉耦合轮廓误差补偿技术.docx
CNC多轴联动的机床交叉耦合轮廓误差补偿技术CNC多轴联动的机床交叉耦合轮廓误差补偿技术摘要:随着现代制造业的发展,对于轮廓精度的要求也越来越高,而传统的机床控制系统中存在着交叉耦合问题导致轮廓误差较大的情况。为此,本文针对CNC多轴联动的机床交叉耦合轮廓误差问题,提出了一种补偿技术。通过建立数学模型,分析了交叉耦合误差的来源和影响因素,并设计了合理的补偿算法,实现了对轮廓误差的补偿,最终得到了更高的加工精度。关键词:CNC机床,多轴联动,交叉耦合,轮廓误差,补偿技术1.引言CNC机床作为现代制造业中的重
数控机床定位误差补偿及其对圆轮廓误差影响分析.docx
数控机床定位误差补偿及其对圆轮廓误差影响分析数控机床的定位误差是指机床在进行加工过程中,由于机床本身的结构、转动系统、传动系统以及热变形等因素,导致其工作台的实际位置与理论位置之间存在一定的偏差。在数控机床中,如何有效地补偿定位误差已经成为了制造业发展的重要课题。一、数控机床定位误差的原因数控机床的定位误差来源很多,其中包括机床的结构问题、传动系统问题、控制系统问题以及加工环境问题。1.机床的结构问题机床的结构问题是导致定位误差的主要因素之一。比如,如果机床的工作台和主轴箱之间存在松动,那么在机床处理高加