
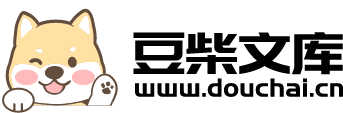
不锈钢焊接技术交底.docx
快乐****蜜蜂
在线预览结束,喜欢就下载吧,查找使用更方便
相关资料
不锈钢焊接技术交底.docx
图纸焊口编号每日焊接焊口输入QC工程师确认抽检探伤工从微机上查找透视焊口探伤探伤结果不合格合格返修资料整理交工QC工程师确认1、焊接施工程序2、施工方法及技术要求2.1施工方法2.1.1焊接材料的选择2.1.1.2304L之间:焊丝采用H00Cr21Ni10;焊条采用A002;2.1.1.3316L之间:焊条采用A022;焊丝采用H00Cr19Ni12Mo2;2.1.2焊接方法Φ≤114mm均采用手工钨极氩弧焊Φ>114mm采用手工钨极氩弧焊打底,手工电弧焊盖面2.1.3对焊工要求2.1.3.1焊工必须按
不锈钢焊接技术交底.doc
图纸焊口编号每日焊接焊口输入QC工程师确认抽检探伤工从微机上查找透视焊口探伤探伤结果不合格合格返修资料整理交工QC工程师确认1、焊接施工程序2、施工方法及技术要求2.1施工方法2.1.1焊接材料的选择2.1.1.2304L之间:焊丝采用H00Cr21Ni10;焊条采用A002;2.1.1.3316L之间:焊条采用A022;焊丝采用H00Cr19Ni12Mo2;2.1.2焊接方法2.1.2.1Φ≤114mm均采用手工钨极氩弧焊2.1.2.2Φ>114mm采用手工钨极氩弧焊打底,
不锈钢管道焊接技术交底记录.docx
SY01-009120万吨/年高硫重油综合利用项目施工技术交底记录单项工程名称:120万吨/年高硫重油综合利用项目单项工程编号:DMXM单位工程名称100万吨/年重油催化制烯烃装置单位工程编号DMCH会议地点会议时间主持人记录人参加单位及人员接受交底人签字:施工技术交底内容:不锈钢管道焊接1、焊前准备:催化管线涉及的不锈钢管道母材材质及要求使用的焊接材料如下表1所示。2、奥氏体不锈钢管道其焊接性能好,在任何温度下都不会发生相变,对氢脆不敏感,在焊态下奥氏体不锈钢接头也有较好的塑性和韧性。3、焊接的主要问题
不锈钢管道焊接技术交底记录.doc
SY01—009120万吨/年高硫重油综合利用项目施工技术交底记录单项工程名称:120万吨/年高硫重油综合利用项目单项工程编号:DMXM单位工程名称100万吨/年重油催化制烯烃装置单位工程编号DMCH会议地点会议时间主持人记录人参加单位及人员接受交底人签字:施工技术交底内容:不锈钢管道焊接1、焊前准备:催化管线涉及的不锈钢管道母材材质及要求使用的焊接材料如下表1所示。2、奥氏体不锈钢管道其焊接性能好,在任何温度下都不会发生相变,对氢脆不敏感,在焊态下奥氏体不锈钢接头也有较好的塑性和韧性。3、焊
不锈钢管道焊接技术交底记录.doc
SY01—009120万吨/年高硫重油综合利用项目施工技术交底记录单项工程名称:120万吨/年高硫重油综合利用项目单项工程编号:DMXM单位工程名称100万吨/年重油催化制烯烃装置单位工程编号DMCH会议地点会议时间主持人记录人参加单位及人员接受交底人签字:施工技术交底内容:不锈钢管道焊接1、焊前准备:催化管线涉及的不锈钢管道母材材质及要求使用的焊接材料如下表1所示。2、奥氏体不锈钢管道其焊接性能好,在任何温度下都不会发生相变,对氢脆不敏感,在焊态下奥氏体不锈钢接头也有较好的塑性和韧性。3、焊