
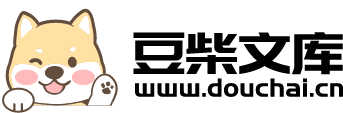
拉刀拉孔缺陷及消除方法..doc
胜利****实阿
在线预览结束,喜欢就下载吧,查找使用更方便
相关资料
拉刀拉孔缺陷及消除方法..doc
拉孔缺陷及消除方法作者赵统钧2、1、1拉削表面产生鳞刺(1)现象:在工件拉出端表面上有鳞片状毛刺,严重影响表面粗糙度,有时增大到Ra25/um。(2)解决途径1)采用低于2m/min或高于5m/min得拉削速度试拉。2)采用较小得齿升量。3)适当增加前角。4)改变材料热处理状态,对低碳钢增加其硬度,中碳钢应降低其硬度等。5)使用极压切削液,尤其就是以含氮得极压切削剂效果最好。2、1、2拉削表面有深浅不一、宽窄不均得犁沟状划痕,最深可达100um、。(1)原因:拉刀切削刃上有积屑瘤,因积屑瘤得形状与高度不断
腰形孔拉刀设计.docx
腰形孔拉刀设计设计任务在拉床上使用拉刀加工工件的工艺过程称为拉削加工。拉削主要用于大批量生产中加工各种形状的通孔、平面及成形面等。拉刀是一种定型刀具,在一次拉削中完成粗切、精切、校准、修光操作,切除被加工表面的全部加工余量,生产率高,加工质量高。但一把拉刀只适宜于一种规格尺寸的孔或槽,拉刀制造复杂,且成本高,只用于大批量生产中。本设计的拉刀用于加工图示的腰形孔,该腰形孔是适用于拉削的典型表面形状。预制腰形孔的情况如图,所用拉床为L6120设计计算根据预制孔的情况及零件图的要求,决定采用同廓式(层拔式)拉削
腰形孔拉刀设计doc.docx
腰形孔拉刀设计南海广播电视大学学习中心邹晔设计任务在拉床上使用拉刀加工工件的工艺过程称为拉削加工。拉削主要用于大批量生产中加工各种形状的通孔、平面及成形面等。拉刀是一种定型刀具,在一次拉削中完成粗切、精切、校准、修光操作,切除被加工表面的全部加工余量,生产率高,加工质量高。但一把拉刀只适宜于一种规格尺寸的孔或槽,拉刀制造复杂,且成本高,只用于大批量生产中。本设计的拉刀用于加工图示的腰形孔,该腰形孔是适用于拉削的典型表面形状。预制腰形孔的情况如图,所用拉床为L6120设计计算根据预制孔的情况及零件图的要求,
腰形孔拉刀设计doc.doc
腰形孔拉刀设计南海广播电视大学学习中心邹晔设计任务在拉床上使用拉刀加工工件的工艺过程称为拉削加工。拉削主要用于大批量生产中加工各种形状的通孔、平面及成形面等。拉刀是一种定型刀具,在一次拉削中完成粗切、精切、校准、修光操作,切除被加工表面的全部加工余量,生产率高,加工质量高。但一把拉刀只适宜于一种规格尺寸的孔或槽,拉刀制造复杂,且成本高,只用于大批量生产中。本设计的拉刀用于加工图示的腰形孔,该腰形孔是适用于拉削的典型表面形状。预制腰形孔的情况如图,所用拉床为L6120设计计算
一种梅花形花键孔的拉刀及拉削工艺.pdf
本发明涉及机械加工技术领域,其公开了一种梅花形花键孔的拉刀及拉削工艺,所述拉刀包括第一夹头段、颈部段、前导段、拉削段、校正段、后导段、尾部段,梅花形切削齿的齿顶沿轴向设有分屑槽,且相邻两个梅花形切削齿上的分屑槽错位设置,所述梅花形切削齿的齿升量按照梅花形切削齿的外径的增加、齿顶宽渐增而分段递减,所述拉刀尾部段的端部轴向开设有一段进油孔,所述校正段上相邻两个梅花形校正齿之间径向开设有连通所述进油孔的出油孔,所述进油孔的孔口安装有油嘴。所述拉削工艺包括采用超声波振动拉削以及拉削时通过拉刀上的出油孔对梅花形校正