
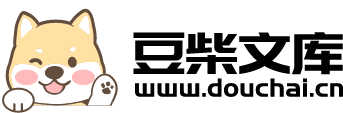
陶瓷结合剂砂轮的制造方法.pdf
羽沫****魔王
在线预览结束,喜欢就下载吧,查找使用更方便
相关资料
陶瓷结合剂砂轮的制造方法.pdf
本发明公开了一种陶瓷结合剂砂轮的制造方法,包括如下步骤:1)制备陶瓷结合剂;2)取10~12质量份陶瓷结合剂、2~3质量份黄糊精、3~5质量份硅酸钠混合,加入球磨机中进行球磨;球磨机中料球重量比为5:1,球磨时间1小时,出料后过筛得到成型料;3)成型料压制砂轮毛坯,并自然干燥2~3天;4)自然干燥后的砂轮毛坯放入烘房进行干燥,先30~40℃干燥48小时,再40~60℃干燥48小时,再60~70℃干燥48小时,最后自然降温至35~40℃;5)烘房干燥后的砂轮毛坯烧成得陶瓷结合剂砂轮。本发明提供的陶瓷结合剂砂
制造陶瓷CBN砂轮的结合剂.pdf
本发明公开了一种制造陶瓷CBN砂轮的结合剂及其制备方法,其改进之处在于所述结合剂其基础配方由下列各组分制成,按重量份数比为:长石30~40份,粘土10~20份,膨润土10~20份,硼玻璃15~25份,荧石8~12份,石英粉4~6份;以基础配方为100%,加入氧化钛5~10%,冰晶石6~8%,碳酸锂8~12%。混合、球磨后进行煅烧,采用分段逐步加温和保温,由常温加温至1350℃,锻烧时间为36小时。本发明有效降低了结合剂的耐火度,提高了抗折强度,使热膨胀系数为与CBN磨料相匹配,所制作的砂轮具有耐热性好、强
一种稀土陶瓷结合剂及使用该结合剂的砂轮的制造方法.pdf
本发明公开了一种稀土陶瓷结合剂,包括稀土氧化物材料、硅质材料、含铝材料和硼酸。本发明还公开了使用该结合剂的砂轮的制造方法,它将稀土氧化物与硅质和含铝材料混合后进行熔炼,经过冷却、球磨、过筛后与磨料混合并进行烧结,烧结后进行车削修整。通过上述方式,本发明能够使砂轮具有高强度、高自锐性、高寿命的三高特点。
复合结合剂砂轮及其制造方法.pdf
本发明涉及磨具磨料领域,具体为复合结合剂砂轮及其制造方法。所用原料包括,磨料、金属粉末、有机结合剂、菱苦土;通过金属复合磨粒的生产、陶瓷金属复合磨粒,再通过有机结合剂压制成型为砂轮坏体,最后固化成为复合结合剂砂轮。本发明采用金属结合剂、菱苦土结合剂、树脂结合剂与磨料颗粒分阶段烧结,最终压制成砂轮,制成的砂轮性能比单一结合剂砂轮有明显提高,而且可减少特殊砂轮的制造成本,扩大砂轮制造中结合剂的品种和砂轮的品种。
树脂结合剂陶瓷刚玉砂轮.pdf
本发明涉及砂轮磨具技术领域,公开了树脂结合剂陶瓷刚玉砂轮,由以下重量份的原料制成:陶瓷刚玉磨料90~110份、酚醛树脂25~35份、冰晶石6~10份、硫化铁5~7份、锡酸锌3~5份、硫酸钙晶须4~8份、碳黑0.5~2份,其中,陶瓷刚玉磨料为采用溶胶‑凝胶法通过烧结制备的陶瓷刚玉磨料。本发明的砂轮本可以降低切割过程对工件的烧伤程度,改善工件烧伤的问题,磨削效率高、发热量小、自锐性强,具有较高的把持力,可以改善工件表面的粗糙度,同时使使用寿命至少提高了50%。