
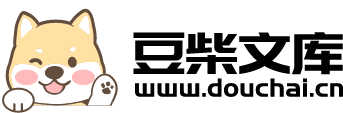
基于模糊神经网络的数控机床热误差补偿技术研究.docx
快乐****蜜蜂
在线预览结束,喜欢就下载吧,查找使用更方便
相关资料
基于模糊神经网络的数控机床热误差补偿技术研究.docx
基于模糊神经网络的数控机床热误差补偿技术研究摘要:本文基于模糊神经网络技术,对数控机床热误差进行了研究,并提出了一种热误差补偿方法。通过实验验证,该方法能够有效地提高数控机床的加工精度和稳定性。文章首先介绍了数控机床的热误差产生原因及其影响,然后分析了模糊神经网络的基本原理,在此基础上提出了热误差补偿方法的实现步骤。最后,通过仿真实验和实际加工试验对该方法进行了验证和分析,结果表明,该方法能够有效地消除热误差的影响,提高数控机床的加工精度和稳定性。关键词:模糊神经网络、数控机床、热误差、补偿技术、加工精度
基于组合神经网络的数控机床热误差补偿建模的研究综述报告.docx
基于组合神经网络的数控机床热误差补偿建模的研究综述报告数控机床是现代工业制造业中最为普遍的生产设备之一,其具有高精度、高效率、自动化等诸多优势,被广泛应用于汽车制造、模具制造、航空航天等领域。然而,随着数控机床的使用时间的增加,其精度往往会受到热误差的影响,导致加工质量下降,影响生产效益。因此,如何精确地预测和补偿机床的热误差成为数控机床研究领域的一个重要问题。神经网络是一种模仿人脑神经系统进行信息处理的计算模型,具有自适应性、非线性映射能力等优势。近年来,基于神经网络的数控机床热误差建模与补偿方法逐渐成
基于遗传算法优化BP神经网络的数控机床热误差补偿.docx
基于遗传算法优化BP神经网络的数控机床热误差补偿论文:基于遗传算法优化BP神经网络的数控机床热误差补偿摘要:在数控机床的加工过程中,热误差是一个重要的影响因素。为了降低热误差带来的影响,本文提出了一种基于遗传算法优化BP神经网络的热误差补偿方法。该方法首先采用传感器获取机床的实时温度数据,并将其与预设的温度进行比较,从而得到热误差数据。然后,利用BP神经网络建立热误差模型,并通过遗传算法对BP神经网络进行优化,以提高其准确性。最后,通过比较实验结果验证了该方法的有效性。关键词:数控机床;热误差;BP神经网
基于神经网络的数控机床误差补偿研究.docx
基于神经网络的数控机床误差补偿研究基于神经网络的数控机床误差补偿研究摘要:数控机床误差补偿是提高数控机床加工精度的重要手段。传统的误差补偿方法往往需要依赖复杂的数学模型,而且对系统参数变化敏感,因此补偿效果不稳定。本文提出一种基于神经网络的数控机床误差补偿方法,在不依赖复杂模型的前提下,通过神经网络学习和预测机床误差,从而实现误差补偿的效果。关键词:神经网络,数控机床,误差补偿1.引言数控机床是现代制造业中不可或缺的设备,其加工精度直接影响产品质量。然而,在实际应用中,由于各种因素的影响,数控机床的加工精
数控机床热误差补偿关键技术研究.docx
数控机床热误差补偿关键技术研究一、引言随着制造技术的不断发展,数控机床成为了现代工业生产的重要设备之一。数控机床具有高精度、高效率、高重复性等特点,已经广泛应用于航空航天、汽车、模具、电子、医疗等行业。尽管数控机床已经在很大程度上解决了传统机床所存在的问题,如工件精度不高、加工效率低等问题,但由于受到各种因素的影响,机床热误差一直是数控机床加工中的重要问题。机床热误差是由于数控机床在加工过程中所受热载荷和环境温度等因素的影响而导致的机床热膨胀引起的误差。热误差会直接影响到加工精度和加工质量,若不及时进行误