
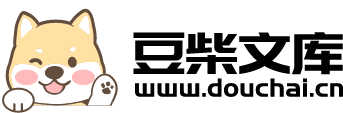
ELID 超精密镜面磨削砂轮磨损规律的研究.docx
快乐****蜜蜂
在线预览结束,喜欢就下载吧,查找使用更方便
相关资料
ELID 超精密镜面磨削砂轮磨损规律的研究.docx
ELID超精密镜面磨削砂轮磨损规律的研究超精密镜面磨削砂轮磨损规律的研究摘要:超精密镜面磨削是一种高精度加工技术,常用于制造精密光学镜面、硬盘等特殊要求的表面。而砂轮在超精密镜面磨削过程中扮演着重要角色,其磨损规律对加工结果和砂轮寿命具有重要影响。本研究旨在深入了解超精密镜面磨削砂轮的磨损规律,为优化磨削过程提供理论依据。关键词:超精密镜面磨削,砂轮,磨损规律1.引言超精密镜面磨削是一种高精度磨削技术,其精度可达亚微米级别甚至纳米级别。超精密镜面磨削广泛应用于制造光学镜片、硬盘和光学导向器等高精度元件。砂
精密和超精密砂轮磨削精密砂轮磨削.ppt
精密与超精密磨料加工用砂轮等磨具对黑色金属、硬脆材料进行磨削加工、研磨加工、抛光加工。软质铜、铝等有色金属一般用金刚石刀具进行超精密切削。第三章精密和超精密磨料加工固结磨料加工:将磨料与结合剂粘结在一起,形成一定的形状和强度,再采用烧结、涂敷等方法制成砂轮、砂带等磨具。用烧结方法制成的砂轮、砂条、油石等称为固结磨具用涂覆方法制成的砂带等称为涂覆磨具主要包括:砂轮磨削、砂带磨削等精密和超精密加工分类游离磨料加工:磨料不固定在一起,成游离状态。传统方法主要包括:研磨、抛光新方法有:磁性研磨、弹性发射加工、磨料
ELID精密镜面磨削系统电源的使用分析.docx
ELID精密镜面磨削系统电源的使用分析ELID(ElectrolyticIn-processDressing)精密镜面磨削是一种高精度和高效率的磨削技术。该技术使用电解过程中产生的氧化物颗粒在磨削中进行自动修整,从而实现精密的表面加工。在ELID技术中,电源是控制整个加工过程的关键元素之一。本文将对ELID精密镜面磨削系统电源的使用进行分析。ELID磨削技术的基本原理是基于电解质在磨料磨削过程中的作用。在ELID技术中,磨削工具与工件之间通过电解质进行连接。磨削时,电解质中会形成氧化物颗粒,在磨削过程中作
铸铁纤维、铸铁结合剂超硬磨料砂轮在ELID超镜面磨削中的应用.docx
铸铁纤维、铸铁结合剂超硬磨料砂轮在ELID超镜面磨削中的应用摘要本文着重研究了铸铁纤维、铸铁结合剂超硬磨料砂轮在ELID超镜面磨削中的应用。随着现代加工技术的不断发展,超精密加工需求不断增加;而ELID超镜面磨削技术以其高效率、高质量的特点受到广泛关注。而铸铁纤维、铸铁结合剂超硬磨料砂轮则是一种优良的研磨工具,其具有自修复和高度耐用的特性。本文利用实验和理论研究,分别从砂轮的成分、砂轮表面的粗糙度、涂层的选择、ELID参数等方面进行了研究。研究结果表明,铸铁纤维、铸铁结合剂超硬磨料砂轮在ELID超镜面磨削
ELID超精密磨削技术综述.doc
8/8ELID超精密磨削技术综述蔡智杰天津大学机械工程学院机械工程系2014级硕士生摘要:金属基超硬磨料砂轮在线电解修整(ElectrolyticIn-processDressing,简称ELID)磨削技术作为一种结合传统磨削、研磨、抛光为一体的复合镜面加工技术,开辟了超精密加工的新途径,具有广发的应用价值。本文将从工作原理、磨削机理、工艺特点、影响因素及磨削机床的分类等方面系统地介绍ELID超精密磨削技术,并通过分析国内外研究应用状况,阐述该技术在精密加工制造行业的应用发展前景。关键词:在线电解修整(E