
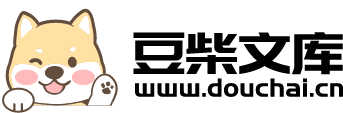
基于BiLSTM的滚动轴承剩余使用寿命预测.docx
快乐****蜜蜂
在线预览结束,喜欢就下载吧,查找使用更方便
相关资料
基于BiLSTM的滚动轴承剩余使用寿命预测.docx
基于BiLSTM的滚动轴承剩余使用寿命预测目录:1.引言2.相关工作3.数据预处理4.模型设计5.实验设计6.实验结果分析7.结论与展望1.引言在工业设备运行中,设备的寿命预测一直是一个重要的课题。随着物联网技术的发展,大量的传感器数据被采集并存储,在此基础上进行设备寿命预测成为可能。其中滚动轴承是一个重要的设备,其故障将导致整个机械系统的失效。因此,滚动轴承的剩余使用寿命预测具有重要的实际意义。本文提出了一种基于BiLSTM的滚动轴承剩余使用寿命预测方法。该方法在数据预处理中采用了滑动窗口的技术,同时根
基于BiLSTM与注意力机制的剩余使用寿命预测研究.docx
基于BiLSTM与注意力机制的剩余使用寿命预测研究基于BiLSTM与注意力机制的剩余使用寿命预测研究摘要:随着工业设备的智能化和自动化的发展,预测剩余使用寿命已成为保障设备可靠性和降低生产成本的重要手段。针对传统的剩余使用寿命预测方法存在的问题,本文提出了一种基于BiLSTM与注意力机制的剩余使用寿命预测方法。通过引入BiLSTM模型可以有效地捕捉序列数据中的时序依赖关系,而注意力机制能够提取关键信息并加强对重要部分的关注。实验结果表明,本文提出的方法在剩余使用寿命预测任务中取得了较好的性能。关键词:剩余
基于LSTM的滚动轴承剩余使用寿命预测.docx
基于LSTM的滚动轴承剩余使用寿命预测标题:基于LSTM的滚动轴承剩余使用寿命预测1.引言-序言引入轴承的重要性和作用-引出轴承剩余使用寿命预测的重要性及挑战-简要介绍LSTM(长短期记忆)模型,以及其在序列预测问题中的应用-指出本文旨在基于LSTM模型实现滚动轴承剩余使用寿命预测2.相关工作-综述目前滚动轴承剩余使用寿命预测的方法和技术-介绍基于机器学习的方法,如支持向量机、神经网络等-分析现有方法的优劣及其在滚动轴承剩余使用寿命预测上的限制-引出LSTM模型在序列预测中的优势,为后续章节奠定基础3.L
基于深度迁移学习的滚动轴承剩余使用寿命预测.docx
基于深度迁移学习的滚动轴承剩余使用寿命预测基于深度迁移学习的滚动轴承剩余使用寿命预测摘要滚动轴承是机械设备中常见的关键部件之一,其损坏可能导致设备故障以及生产线停机。因此,实时监测和准确预测滚动轴承的剩余使用寿命对于设备的维护和故障预防具有重要意义。本论文提出了一种基于深度迁移学习的方法来预测滚动轴承的剩余使用寿命,通过将特征从一个源领域转移到另一个目标领域来提高预测性能。实验结果表明,该方法在滚动轴承寿命预测方面取得了较好的准确性和鲁棒性。1.引言滚动轴承在机械设备中起着至关重要的作用,但随着使用时间的
基于注意力TCN的滚动轴承剩余使用寿命预测方法.pptx
汇报人:CONTENTS添加章节标题注意力机制与滚动轴承剩余使用寿命预测注意力机制原理注意力机制在轴承寿命预测中的应用注意力TCN模型构建模型训练与优化滚动轴承性能退化分析轴承性能退化数据采集性能退化特征提取特征选择与降维退化状态评估基于注意力TCN的剩余使用寿命预测模型模型输入与输出模型训练与验证预测结果评估模型优化与改进实验结果与分析实验设置与数据集实验结果对比分析模型性能评价指标结果讨论与解释结论与展望研究成果总结未来研究方向技术应用前景汇报人: