
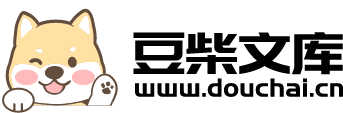
第二节--砂型铸造及工艺方案的选择-砂型铸造是以砂为主要造型材料制备铸型的一种铸造方法。铸型由砂型和砂.ppt
lj****88
亲,该文档总共61页,到这已经超出免费预览范围,如果喜欢就直接下载吧~
相关资料
第二节--砂型铸造及工艺方案的选择-砂型铸造是以砂为主要造型材料制备铸型的一种铸造方法。铸型由砂型和砂.ppt
第二节砂型铸造及工艺方案的选择砂型铸造生产过程砂型铸造的工艺过程一)、造型材料二)模样与芯盒三)造芯及合箱四)铸铁的熔炼及浇注五)落砂、清理和检验二、砂型铸造的造型方法造型是砂型铸造最基本的工序,造型方法选择的是否合理,对铸件质量和成本有着重要的影响.一)手工造型:填砂、紧实和起模由人工完成优点:操作灵活,适用性强,模型成本低,生产准备时间短.缺点:铸件质量差,生产率低,劳动强度高.应用:单件,小批.零件part手工造型的两箱造型图解手工造型方法:整模造型、分模造型、挖砂造型、假箱造型、三箱造型、活块造型
砂型铸造的造型工艺.pptx
会计学铸造:将液态金属浇注到铸型型腔中,待其冷却凝固后,获得一定形状的毛坯或零件的方法。铸造生产的特点:优点——零件的形状复杂;工艺灵活;成本较低。缺点——机械性能较低;精度低;效率低;劳动条件差。分类:砂型(shāxíng)铸造——90%以上特种铸造——铸件性能较好,精度低,效率高我国铸造技术历史悠久,早在三千多年前,青铜器已有应用;二千五百年前,铸铁工具已经相当普遍。泥型、金属型和失蜡型是我国创造的三大铸造技术。第一节砂型(shāxíng)铸造的造型工艺铸造生产(shēngchǎn)常规工艺流程/一、
砂型铸造的造型工艺.pptx
第二章铸造工艺基础知识铸造:将液态金属浇注到铸型型腔中,待其冷却凝固后,取得一定形状旳毛坯或零件旳措施。铸造生产旳特点:优点——零件旳形状复杂;工艺灵活;成本较低。缺陷——机械性能较低;精度低;效率低;劳动条件差。分类:砂型铸造——90%以上特种铸造——铸件性能很好,精度低,效率高我国铸造技术历史悠久,早在三千数年前,青铜器已经有应用;二千五百年前,铸铁工具已经相当普遍。泥型、金属型和失蜡型是我国发明旳三大铸造技术。第一节砂型铸造旳造型工艺铸造生产常规工艺流程一、砂型铸造工艺(一)型砂和芯砂旳制备砂型铸造
一种砂型铸造造型工艺.pdf
本发明公开了一种砂型铸造造型工艺,涉及铸造技术领域,包括以下步骤:将两个型号一致铸件分别放入均设有升降机构且设有分界面的上安放座和下安放座中;通过升降机构将两个铸件上升到露出到分界面外;造下型:在下安放座上方安装下砂箱,填充树脂自硬砂,得到下砂型;造上型:在上安放座上方安装上砂箱,填充树脂自硬砂,并插入浇口棒,得到上砂型;拆除上砂箱和下砂箱,取出上砂型和下砂型;对铸件进行落砂处理,并通过升降机构将铸件完全降到分界面下,本发明的铸造工艺区别于挖砂造型和假箱造型,运用到了挖坑造型的原理,却不需要在地面预留坑,
一种砂型铸造筛砂机.pdf
本发明涉及一种砂型铸造筛砂机,它包括内筛筒和外筒,内筛筒的外侧设置有外筒,外筒的侧面设置有控制面板,外筒的下方设置有前支腿和后支腿,前支腿均由活塞杆和液压缸组成,后支腿均铰接在外筒底部,外筒的下方开设有出砂口,出砂口上设置有挡砂板,挡砂板的下方设置有集砂槽,内筛筒的前方焊接有进料口,进料口和内筛筒交接处设置有电磁阀,进料口的下方设置有电机,电机连接有转轴,转轴上设置有搅拌桨,转轴的前后方上均设置有内花键,内筛筒的前后方上均设置有与内花键相配套使用的外花键,外筒的前后方上均设置有轴承,内筛筒的下方开设有废料