
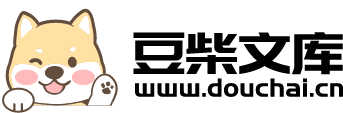
内滚道缺陷对滚动轴承刚度特性的影响研究.docx
骑着****猪猪
在线预览结束,喜欢就下载吧,查找使用更方便
相关资料
内滚道缺陷对滚动轴承刚度特性的影响研究.docx
内滚道缺陷对滚动轴承刚度特性的影响研究摘要:随着技术的不断发展,滚动轴承作为重要的机械零部件在各行业中得到了广泛的应用。而轴承的刚度特性又是影响其工作性能和寿命的重要因素之一。本文研究了内滚道缺陷对滚动轴承刚度特性的影响,分析了不同类型缺陷对轴承刚度的影响,为轴承缺陷检测和轴承设计提供了一定的参考。关键词:滚动轴承;刚度特性;内滚道缺陷;缺陷检测;轴承设计一、引言滚动轴承作为机械传动中的重要零部件,其工作性能和寿命关系着机械设备和产品的质量和使用寿命。而轴承的刚度特性,也是机械传动中的关键因素,它影响着轴
轴承滚道局部故障与其振动特性的影响研究.docx
轴承滚道局部故障与其振动特性的影响研究轴承作为机械传动中的重要部件,其质量和运转状态对整个传动系统以及设备的稳定性和可靠性有着重要的影响。在轴承的整个运转过程中,滚道的状态是直接决定轴承性能和寿命的一个关键因素。在轴承滚道局部故障的情况下,不仅会影响轴承的摩擦和转动,还会导致轴承和传动系统的振动性能发生明显变化。轴承滚道局部故障的类型主要包括表面痕迹、微裂纹、金属疲劳、碰撞等等。不同类型的局部故障对轴承的影响也各不相同。以表面痕迹为例,由于轴承滚动时表面间的接触应力较大,当出现局部表面痕迹后,就会导致局部
单点缺陷滚动轴承的力学行为与响应特性研究.docx
单点缺陷滚动轴承的力学行为与响应特性研究摘要:本研究通过理论分析和数值模拟,探讨单点缺陷对滚动轴承的力学行为和响应特性的影响。研究结果表明,单点缺陷会导致轴承刚度和载荷承受能力的降低,进而引起轴承的振动和噪声。同时,单点缺陷的位置、尺寸和形状对轴承的性能影响非常显著。本文通过对轴承力学行为和响应特性的研究,为轴承设计和维护提供了一定的参考。关键词:单点缺陷;滚动轴承;力学行为;响应特性引言:滚动轴承是广泛应用于各种机械设备中的重要元件。在工作过程中,轴承承受着各种载荷并转移旋转运动,扮演着“承重转动”的重
扣件刚度对钢轨振动特性的影响研究.docx
扣件刚度对钢轨振动特性的影响研究扣件刚度对钢轨振动特性的影响研究摘要:钢轨是铁路运输系统中的重要组成部分,其振动特性直接影响运输系统的安全和运行效率。本论文研究了扣件刚度对钢轨振动特性的影响。通过实验和数值模拟,比较了不同刚度扣件的振动特性差异,并探讨了扣件刚度与钢轨振动频率的关系。研究结果表明,增加扣件刚度能有效减小钢轨的振动幅值和频率,提高铁路运输系统的稳定性和安全性。1.引言钢轨是铁路运输系统中的关键结构之一,其振动特性直接影响铁路运输系统的安全和运行效率。扣件是固定钢轨的重要组成部分,其刚度对钢轨
扣件刚度对钢轨振动特性的影响研究.pptx
汇报人:目录PARTONEPARTTWO扣件刚度的定义扣件刚度在轨道中的作用扣件刚度对列车运行安全的影响PARTTHREE钢轨振动产生的原因钢轨振动的危害钢轨振动与扣件刚度的关系PARTFOUR扣件刚度对钢轨振动频率的影响扣件刚度对钢轨振动幅值的影响扣件刚度对钢轨振动持续时间的影响扣件刚度对钢轨振动模式的影响PARTFIVE实验设计实验过程与数据采集实验结果分析结果与实际应用的结合PARTSIX研究结论总结对扣件刚度的建议调整方案对未来研究的展望THANKYOU