
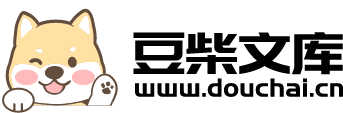
异步错距旋压加工方法.pdf
哲妍****彩妍
在线预览结束,喜欢就下载吧,查找使用更方便
相关资料
异步错距旋压加工方法.pdf
一种异步错距旋压加工方法,结合张力旋压、异步轧制与错距旋压原理,在正向错距旋压时,利用前旋轮的进给速度大于后旋轮的进给速度,在两旋轮间的变形区人为制造拉力,形成张力旋压,由于前旋轮于后旋轮的进给速度不同步,故称为异步错距旋压。利用各旋轮可独立进给的旋压机,在旋压过程中采用两旋轮或者三旋轮轴向错距且进给速度不同的方法进行加工,成形高精度筒形旋压结构件。
一种筒形件错距旋压加工旋轮错距量的调整方法.pdf
一种筒形件错距旋压加工旋轮错距量的调整方法,在充分考虑坯料受力均衡性的基础上,根据旋压毛坯形状尺寸及首道次压下量精确确定旋轮轴向错距量以改善现有技术的不足,避免在调整旋轮轴向错距量时存在的盲目性和不确定性,确保起旋时旋轮能同时与毛坯接触,提高了筒形件错距旋压的稳定性和成形精度。试验证明,本发明所阐述的错距量调整方法对旋轮进行轴向调整,然后进行旋压,结果显示:筒形件的直线度提高约10%,壁厚差减小约5%,有效使用长度增加约5%。
错距旋压筒形件的工艺方法.pdf
本发明为一种错距旋压筒形件的工艺方法,将三个旋轮初始设置于同一水平面,采用三个旋轮同步径向进刀、同步下移并同时与旋压坯料顶端接触,在三个旋轮接触到旋压坯料顶端且工艺状态稳定后,三个旋轮再依次按相同的轴向错距量逐渐错开直到设定的距离,旋轮在轴向运动的同时径向进给,且压下量逐渐增加直到设定值,最后进行错距旋压成形。本发明的工艺方法可以使芯模始终承受三个旋轮的旋压力,从而避免芯模受力不平衡,产生弯矩影响成形;进而,在有效提高生产效率的同时,减小主轴承受的弯矩,保证主轴精度不变,延长主轴使用寿命,提高零件壁厚精度
一种调节三旋轮旋压错距量的方法.pdf
一种调节三旋轮旋压错距量的方法,在设定各旋轮减薄量时,依据材料的加工硬化规定了三旋轮错距旋压时各旋轮的减薄量。根据总减薄量T以及旋轮数量、各旋轮错距旋压时减薄量分配值,得到各旋轮减薄量。在调整各旋轮的轴向位置时,将各旋轮沿筒形件径向移动至旋压毛坯相应的壁厚减薄量区域,使各旋轮旋入角α边所在直线均与第一个旋轮旋入角α边所在直线相切,得到各旋轮间错距量,精度达到0.01mm级。本发明将多个旋轮等效为一个台阶式整体旋轮,实现金属材料的稳定变形;在确定各旋轮间错距量时,充分考虑了材料及设备的回弹、各旋轮减薄量的分
一种调节两旋轮旋压错距量的方法.pdf
一种调节两旋轮旋压错距量的方法,在设定各旋轮减薄量时,依据材料的加工硬化规定了三旋轮错距旋压时各旋轮的减薄量。根据总减薄量T以及旋轮数量、各旋轮错距旋压时减薄量分配值,得到各旋轮减薄量。在调整各旋轮的轴向位置时,将各旋轮沿筒形件径向移动至旋压毛坯相应的壁厚减薄量区域,使各旋轮旋入角α边所在直线均与第一个旋轮旋入角α边所在直线相切,得到各旋轮间错距量,精度达到0.01mm级。本发明将多个旋轮等效为一个台阶式整体旋轮,实现金属材料的稳定变形;在确定各旋轮间错距量时,充分考虑了材料及设备的回弹、各旋轮减薄量的分