
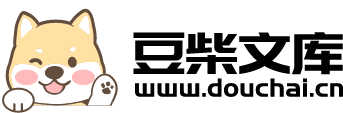
一种大型轮槽半精铣刀及其加工方法.pdf
论文****酱吖
在线预览结束,喜欢就下载吧,查找使用更方便
相关资料
一种大型轮槽半精铣刀及其加工方法.pdf
一种大型轮槽半精铣刀及其加工方法,它涉及一种铣刀及其加工方法。大型轮槽粗半精铣刀因其结构复杂使其加工过程步骤繁琐,操作复杂且难以保证加工精度。本发明中正棒本体的一端为ISO40锥柄,正棒本体的另一端为型线端,该端沿正棒本体的轴向方向均匀加工有多个齿背台阶,多个齿背台阶的外圆从靠近ISO40锥柄的一端至远离ISO40锥柄的另一端依次递减,每两个相邻齿背台阶之间加工有一个容屑槽,多个齿背台阶通过多个容屑槽均匀分割形成多个沿正棒本体的轴向方向设置的磨铲齿,每个磨铲齿的后刀面的形状为连续的圆弧形,正棒本体的中部加
一种汽轮机转子轮槽半精铣刀及其加工方法.pdf
本发明涉及机械加工领域,旨在现有轮槽铣刀存在不能兼顾切削速度和结构强度的问题,提供一种汽轮机转子轮槽半精铣刀及其加工方法,切削刃的前刀面为负棱边刃型面,前刀面在切削刃线的波谷处法向前角在0°~‑5°内变化,在横向中轴附近在‑5°~‑10°内变化,在波峰处在‑10°~‑15°内变化;依据离散单元特征刀具寿命设计理念,通过离散切削单元切削仿真模拟,初步确定前角大小,再利用初定的前角大小制成单元切削刀具,通过单元切削实验效果,精确设计切削前角大小;各切削刃的后刀面上分布有沿切削刃线延伸方向依次分布的加工槽,加工
一种轮槽铣刀车削加工方法.pdf
一种轮槽铣刀车削加工方法,它涉及一种车削加工方法,具体涉及一种轮槽铣刀车削加工方法。本发明为了解决目前还没有一种加工方法能保证轮槽铣刀型线轴向尺寸一致的问题。本发明的具体步骤为:现在普通车床上加工轮槽铣刀;再将轮槽铣刀安装在车削夹具上,用数控车床上用55°菱形车刀片半精车轮槽铣刀型线;然后采用35°菱形车刀片精车轮槽铣刀型线;加工完毕后,从车削夹具上取下轮槽铣刀。本发明用于车削轮槽铣刀。
半封闭凹槽的槽铣刀、加工刀具及加工方法.pdf
本发明涉及半封闭凹槽的槽铣刀,包括刀杆,所述刀杆包括用于伸入盲孔的直径较小的工作端以及位于盲孔外的直径较大的夹持端,所述工作端的尾部安装有一片沿径向的槽铣刀片。本发明还涉及半封闭凹槽的加工刀具及加工方法。本发明槽铣刀的刀杆直径在夹持端大、工作端端小,有利于工作时减少震动,而刀杆上仅安装一片刀片,单位时间切削量少,振动小,有利刀的保护;依次利用三把该种结构的槽铣刀对半封闭凹槽加工,每把槽铣刀工作端外周边缘与刀片刀刃处的距离依次增加,能够在完成深槽加工的同时保护刀具,延长其使用寿命。本发明可应用于径向加工深度
一种汽轮机转子轮槽半精铣刀.pdf
本发明公开了一种汽轮机转子轮槽半精铣刀,包括:刀柄、容屑槽和切削刃;所述容屑槽的螺旋角贯穿全部切削刃;其特征在于:所述切削刃前刀面设计有负棱边,法向前角沿型线轮廓根据各点切削余量变化而不同,所述切削刃后刀面为尖齿结构。本发明采用负棱边设计理念开发,抗崩刃性能非常优异,有效增强了刀具可靠性,大幅度提高了刀具效率和耐用度。