
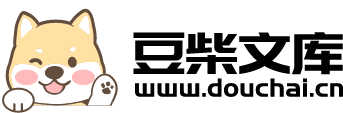
带法兰凸缘轮辋挤扩成形方法.pdf
是翠****ng
在线预览结束,喜欢就下载吧,查找使用更方便
相关资料
带法兰凸缘轮辋挤扩成形方法.pdf
一种带法兰凸缘轮辋挤扩成形方法,其特征在于包括如下步骤:①下料工序;②加热工序,对经下料工序的棒料和挤压模具分别加热至开挤温度;③双向挤扩成形工序。与现有技术相比,本发明的优点在于:工序少,成套成形工装和设备投入,适合工业化批量生产;缩短了成形周期,提高了成形效率;降低了制造成本。
具有优化的轮辋凸缘形状的车轮轮辋.pdf
一种用于轮胎的轮辋(3),所述轮辋具有旋转轴线DD',所述轮辋具有轮辋座(31),所述轮辋座(31)通过轮辋凸缘(32)轴向地向外延伸,所述轮辋凸缘(32)具有第一部分(321),所述第一部分(321)基本上定向在相对于所述轮辋座(31)的垂直平面中并且在径向上位于外部,其特征在于,所述轮辋凸缘(32)具有第二部分(322),所述第二部分(322)朝向外部倾斜,所述第二部分(322)相对于所述第一部分(321)在轴向上位于外部,所述第二部分(322)相对于所述轮辋座(31)至少部分地在径向上位于外部;所述
具有高度降低的轮辋凸缘的轮辋.pdf
一种轮辋(3),其用于具有柔性延长件的滚动组件,所述轮辋具有旋转轴线DD',所述轮辋具有轮辋座(31),所述轮辋座(31)通过轮辋凸缘(32)轴向地向外侧延伸,所述轮辋凸缘(32)具有第一部分(321),所述第一部分(321)基本上定向在垂直于旋转轴线DD'的平面中并且位于相对于所述轮辋座(31)的径向外侧,所述第一部分(321)通过连接部分在径向上和轴向上朝向外侧延伸,其特征在于,在轮辋座的迹线与第一部分的迹线之间的交点与所述轮辋凸缘(32)的径向最外侧部分的端部之间测得的径向高度小于10mm。
轮辋凸缘装饰环维修系统.pdf
本发明提供了一种适于连接至适于支承轮胎的轮辋凸缘的轮辋凸缘装饰环,该轮辋包括圆柱体部分,其包括第一末端和第二末端,第一和第二末端在径向向外延伸的轮辋中分别终结。该轮辋凸缘装饰环包含具有U形横截面的总体环状体,轮辋凸缘装饰环适于置于所述轮辋凸缘上并容纳所述轮辋凸缘。
带凸缘台阶零件的成形工艺.docx
带凸缘台阶零件的成形工艺标题:带凸缘台阶零件的成形工艺摘要:本文主要研究带凸缘台阶零件的成形工艺。首先介绍了带凸缘台阶零件的定义和应用领域,然后探讨了凸缘和台阶对成形工艺的影响,并介绍了常见的成形工艺,包括冲压成形、注塑成形和粉末冶金成形。针对不同成形工艺,论文详细分析了各自的特点、优缺点以及适用范围,并对不同成形工艺的选择进行了比较和评估。最后,提出了带凸缘台阶零件成形工艺的发展趋势和未来的研究方向。关键词:带凸缘台阶零件;成形工艺;冲压成形;注塑成形;粉末冶金成形1.引言带凸缘台阶零件是一种常见的零件