
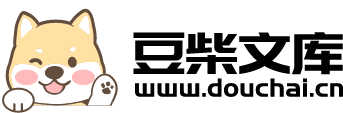
一种立式注塑机自动上料系统的落料装置.pdf
一吃****新冬
在线预览结束,喜欢就下载吧,查找使用更方便
相关资料
一种立式注塑机自动上料系统的落料装置.pdf
本发明公开了一种立式注塑机自动上料系统的落料装置,工作时,金属构件大头朝上小头朝下,一个挨一个进入空槽结构的输送导轨,由于输送导轨受电磁振动力,使金属构件作向前的抛物跳跃运动,直到进入齿盘的齿槽内,分布在导轨两侧的第一步进电机驱动齿盘转动,从而将齿槽内的金属构件逐个拨入落料套内,进而落入储料器的储料孔内,储料器每次装入两个金属构件,第二步进电机通过齿轮齿条传动使储料器向前运动一个落料工位,从而重复装载两个金属构件,直到储料器上的储料孔全部装完为止,最后,振动器启动以保证储料器每个金属构件都能准确竖直地插入
一种自卸式落料装置.pdf
本发明提供了一种自卸式落料装置,其使得钢球自动落向入料装置,无需人工运送、干预,其省时省力、效率高,保证了钢球的准确运送。其包括进料斗,所述进料斗的下方通向带除尘装置,其特征在于:所述进料斗的上方设置有输送料条,所述输送链条上装有运料车,所述运料车包括运料斗、导向板、翻转轴承,所述运料斗的外侧设置有导向板,所述运料斗的上部中心靠前位置的两侧贯穿有所述翻转轴承,所述翻转轴承、导向板、运料斗三者形成固定位置关系的所述运料车,所述翻转轴承支承于所述输送链条的定位槽内,所述运料斗为上大下小的收口结构。
一种散料连续取料装置和自动上料系统.pdf
本发明公开了一种散料连续取料装置和自动上料系统,该取料装置包括机架、挠性输送皮带、驱动轮组件、涨紧轮组件、下换向滚轮、以及上换向轮组件,所述挠性输送皮带的工作面包括倾斜的取样段、平直过渡段和呈大仰角配置的筛选段,还包括:平直托板和换向托板,位于挠性输送皮带的工作面底部,用于支撑所述挠性输送平台的工作面;以及平直压边板和换向压边板,位于挠性输送皮带沿宽度方向两侧,对所述挠性输送皮带的工作面进行压边。本发明提供了一种松散小物料无卡滞、无漏料且连续稳定定量供料的解决方案,本自动上料系统具有低噪音、储料量大、连续
一种小料称量配料系统自动上料装置.pdf
本发明涉及一种小料称量配料系统自动上料装置,包括:计量料桶、输送装置、放料装置、第一负压装置,放料装置上设置有楼梯,放料装置和输送装置分别与控制装置连接,放料装置的顶部设置有送料口,自动上料装置位于送料口的上方,包括底座支架,底座支架为三角结构,底座支架的一端设置有液压缸,另两端分别设置有上料支撑架,上料支撑架之间通过支撑板连接,上料支撑架的顶部与送料槽的上端通过铰链连接,送料槽的下端与液压缸连接,送料槽的底部设置有料仓,送料槽的顶部设置有驱动电机,送料槽内设置有第一旋转轴,驱动电机通过皮带与第一旋转轴连
一种均匀落料系统及落料方法.pdf
本发明公开了一种均匀落料系统及其使用方法,分装机构,分装机构包括支撑架,支撑架上方设置有上输送带,上输送带包括第一上输送带和第二上输送带,第一上输送带上方设置有漏斗,第一上输送带和第二上输送带相互配合使上输送带上表面形成一个平面,第一上输送带内设置有振动器,第二上输送带右端设置有红外线检测装置;上输送带下方设置有下输送带,下输送带高度和托盘出口高度相适配,下输送带用于输送托盘,支撑架右端连接有第二推杆电机,第二推杆电机设置在下输送带的一侧用于限制托盘运动;下输送带的速度大于上输送带的速度。本发明操作简单,