
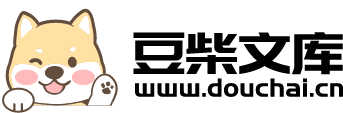
一种复合梯度耐磨合金层及其制备方法.pdf
努力****幻翠
亲,该文档总共12页,到这已经超出免费预览范围,如果喜欢就直接下载吧~
相关资料
一种复合梯度耐磨合金层及其制备方法.pdf
本发明公开了一种复合梯度耐磨合金层及其制备方法,所述Mo/WC复合结构的梯度陶瓷耐磨合金层包括三个区域,分别为无孔洞杂质、呈致密堆砌结构的Mo‑W沉积层,成分、结构均由表及里呈梯度分布的Mo/WC陶瓷层及颗粒均匀、组织致密的离子注入C强化层。所述制备方法包括:第一步,离子注入C;第二步,通过双层辉光等离子合金化技术制备W‑Mo合金层。本发明相较于其他提高粉末冶金齿轮耐磨性能的方法,克服了单一技术存在的问题,实现了技术优势最大化,有利于显著提高粉末冶金齿轮的耐磨性能,有利于延长齿轮的使用寿命。
一种Ti/CrN复合结构的梯度陶瓷耐磨合金层及其制备方法.pdf
本发明公开了一种Ti/CrN复合结构的梯度陶瓷耐磨合金层及其制备方法,该合金层自上而下依次包括Ti‑Cr沉积层、Ti/CrN梯度陶瓷层和N强化层。其制备方法为:(1)在粉末冶金齿轮表面离子注入N强化层;(2)在N强化层表面用双辉等离子合金化法制备Ti‑Cr合金层。氮原子易与合金元素发生相互作用,形成的氮化物可提高耐磨性能。在等离子合金化过程中,溅射出的Ti、Cr离子与离子注入的N发生反应,形成了Ti/CrN复合结构的梯度陶瓷耐磨合金层。相较于其他提高粉末冶金齿轮耐磨性能的方法,本发明实现了两种技术优势最大
一种Ti(C、N)/Cr(C、N)复合梯度耐磨合金层及其制备方法.pdf
本发明公开了一种Ti(C、N)/Cr(C、N)复合梯度耐磨合金层及其制备方法,该合金层自上而下依次包括Ti‑Cr沉积层、Ti(C、N)/Cr(C、N)梯度陶瓷层和C、N强化层。制备方法包括以下步骤:(1)在粉末冶金齿轮表面离子注入C、N强化层;(2)在C、N强化层表面用双辉等离子合金化法制备Ti‑Cr合金层。C、N原子易与合金元素发生相互作用,产生氮化物、碳化物。在等离子合金化过程中,溅射出的Ti、Cr与离子注入的C、N发生反应,形成了具有Ti(C、N)/Cr(C、N)复合结构的梯度陶瓷耐磨合金层。本发明
一种钛合金梯度复合材料及其制备方法.pdf
本发明公开了一种钛合金梯度复合材料及其制备方法,其制备方法如下:(1)选择常规钛合金为基础合金,锆基金属玻璃或钛基金属玻璃为热浸合金;(2)利用非自耗电弧炉将热浸合金熔炼成合金锭,并破碎研磨成粉末;(3)将钛合金和热浸合金粉末放入坩埚内,感应加热至热浸合金熔化,使固相钛合金与热浸合金液发生冶金反应;(4)实施快速顺序凝固,使熔融态的热浸合金液快速冷却形成金属玻璃及其复合材料,进而获得一种由钛合金心部、金属玻璃复合材料过渡层及单相金属玻璃表面层构成的梯度复合材料。本发明的钛合金梯度复合材料具有优异的耐磨损性
一种功能梯度耐磨铁基复合材料及其制备方法.pdf
本发明提出了一种功能梯度耐磨铁基复合材料及其制备方法,由母体金属与若干圆锥状增强体构成,圆锥状增强体的底部位于母体金属上表面,由表及里增强相的体积分数逐渐越小,增强体通过陶瓷颗粒预制体与母液金属的熔渗而形成。制备方法包括:设计并制备石墨模具;将陶瓷颗粒与金属粉末使用无水乙醇机械混合均匀得到混合物,将上述混合物填充于石墨模具中,烘干,然后将模具和混合颗粒一起放入真空烧结炉内烧结。金属粉末将陶瓷颗粒粘结在一起,冷却后打开模具,将成型后的预制体取出;将圆锥状预制体放于铸型底部;炉熔炼铁基金属,对铸型型腔造成负压