
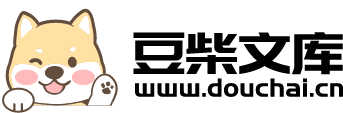
垫片课程设计冲压模具.doc
sy****28
在线预览结束,喜欢就下载吧,查找使用更方便
相关资料
垫片冲压模具课程设计.doc
设计规定:设计该零件旳冲裁模冲压件图如下图所示冲压技术规定:材料:H62材料厚度:4mm生产批量:中批量未注公差:按IT14级确定.2.零件旳工艺性分析.2.1零件旳工艺性分析该零件材料为H62(黄铜)构造简朴,形状对称,凹模宽度B=12≥1.2t(t为材料厚度),冲孔时有尺寸为φ6.5>φ5.2根据书本P86页知冲孔时,因受凸模强度旳限制,孔旳尺寸不应太小.冲孔旳最小尺寸取决于材料性能,凸模旳强度和模具构造等.根据表3-3可查得圆形孔最小值得d=0.9t=0.9X4=3.6mm<φ5.2因此满足工艺性规
垫片课程设计冲压模具.doc
冲压模具设计说明书一、课题名称:垫片落料复合模课题名称:二、设计要求:设计要求:1.主要内容(1)编制冲压工艺(2)设计模具(分析、计算、装配图、非标零件图)(3)编制模具主要零件制造工艺(4)分析估算工时,确定完成工期(5)核算成本,报价(6)编写全套设计制造说明书2.基本要求:(1)分析计算全面,图纸表达准确;(2)工艺水平规程制定,力求符合实际;(3)必要的数据须进行市场调查;(4)分析核算工期、成本,着重于过程。3.课题某定单,圆形垫片100万件,结构如图所示,材料Q235,t=1.0mm。精度要
垫片课程设计冲压模具1.doc
重庆大学机械学院课题设计垫片落料复合模一、课题名称:垫片落料复合模二、设计要求:1.主要内容(1)编制冲压工艺(2)设计模具(分析、计算、装配图、非标零件图)(3)编制模具主要零件制造工艺(4)分析估算工时,确定完成工期(5)核算成本,报价(6)编写全套设计制造说明书2.基本要求:(1)分析计算全面,图纸表达准确;(2)工艺水平规程制定,力求符合实际;(3)必要的数据须进行市场调查;(4)分析核算工期、成本,着重于过程。3.课题某定单,圆形垫片100万件,结构如图所示,材料Q235,t=1.0mm。精度要
方形垫片连续模具课程设计冲压模具.doc
PAGE\*MERGEFORMAT212020年4月19日方形垫片连续模具课程设计冲压模具文档仅供参考,不当之处,请联系改正。冲压模具设计说明书一、课题名称:垫片冲孔落料连续模二、设计要求:1.主要内容(1)编制冲压工艺(2)设计模具(分析、计算、装配图、非标零件图)(3)编制模具主要零件制造工艺(4)分析估算工时,确定完成工期(5)核算成本,报价(6)编写全套设计制造说明书2.基本要求:(1)分析计算全面,图纸表示准确;(2)工艺水平规程制定,力求符合实际;(3)必要的数据须进行市场调查;(4)分
模具课程设计垫片冲压模具设计.docx
模具课程设计垫片冲压模具设计学校:电子科技大学中山学院学院:机电工程学院班级:09机械C班姓名:许桂林学号:29100101062指导老师:刘海潮2013年1月5日冲压模设计题目如图1所示零件:垫扳生产批量:大批量材料:08Ft=2mm设计该零件的冲压工艺与模具垫板冲压模具课程设计摘要:本设计为一垫板的冷冲压模具设计,根据设计零件的尺寸、材料、批量生产等要求,首先分析零件的工艺性,确定冲裁工艺方案及模具结构方案,然后通过工艺设计计算,确定排样和裁板,计算冲压力和压力中心,初选压力机,计算凸、凹模刃口尺寸和