
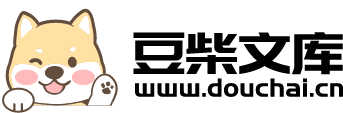
基于多尺度特征融合的卷积孪生点网络叶片轮廓拼接系统.pdf
景福****90
亲,该文档总共12页,到这已经超出免费预览范围,如果喜欢就直接下载吧~
相关资料
基于多尺度特征融合的卷积孪生点网络叶片轮廓拼接系统.pdf
本发明公开了基于多尺度特征融合的卷积孪生点网络叶片轮廓拼接系统,包括数据采集模块、卷积孪生点网络和数据拼接模块,所述卷积孪生点网络包括迭代数次的网络模块,网络模块包括特征提取模块、特征空间匹配模块和奇异值分解模块;所述特征提取模块采用改进型金字塔结构的边缘卷积网络结构提取源点云和目标点云中的高维空间特征,再利用高维空间特征计算出特征空间匹配矩阵,利用该特征空间匹配矩阵计算出两点云数据(源点云和目标点云)中点的对应关系,最后通过奇异值分解求出两点云数据(源点云和目标点云)间的刚体转化,根据多次迭代求解出最优
基于多空间相似度的卷积双胞胎点网络叶片轮廓拼接系统.pdf
本发明公开了基于多空间相似度的卷积双胞胎点网络叶片轮廓拼接系统,包括数据采集模块、卷积双胞胎点网络和数据拼接模块,卷积双胞胎点网络包括迭代数次的网络模块,网络模块包括特征提取模块、匹配矩阵模块、注意力机制模块和奇异值分解模块;特征提取模块采用边缘卷积网络结构提取源点云和目标点云中的高维空间特征,再利用高维空间特征和坐标空间分别计算出特征空间匹配矩阵和坐标空间匹配矩阵,然后通过注意力机制处理特征空间匹配矩阵和坐标空间匹配矩阵之间的冲突得到最终的匹配矩阵,通过最终的匹配矩阵计算出源点云和目标点云中点的对应关系
基于多尺度特征融合空洞卷积网络的手写中文识别方法.pdf
本发明属于识别方法技术领域,具体涉及基于多尺度特征融合空洞卷积网络的手写中文识别方法,使用CASIA‑HWDB1.1数据集作为模型训练与测试数据集;对数据的二值化与归一化处理;对数据标签进行处理,得到One‑Hot形式的数据标签,供网络进行训练;将数据以K折交叉方法划分为多个训练集‑测试集组合;构建识别网络;使用训练集数据对网络进行参数的优化训练;使用K折交叉得到的多个数据集获取最优模型;使用准确率、召回率与F1‑Score对模型进行评价。本发明基于深度神经网络构建了手写字识别模型,模型无需进行人工特征工
一种基于卷积网络多尺度特征融合的鞋印身高估计方法.pdf
本发明提供了一种基于卷积网络多尺度特征融合的鞋印身高估计方法,属于刑事侦查技术领域。技术方案:将鞋印旋转校正;将鞋印进行中心化处理;对异常数据进行处理;将鞋印数据增广;通过多尺度特征提取网络对图像进行处理;通过金字塔特征融合网络对图像进行处理;通过全局结构特征提取网络对图像进行处理;通过身高回归预测网络输出预测身高。有益效果:本发明使用多尺度特征提取网络提取出不同尺度的图像特征并通过金字塔特征融合网络进行多尺度特征融合,最大限度地保留了图像中深层的特征语义信息特征和浅层的空间信息特征;保证泛化能力的基础上
基于多尺度特征融合网络的二维手部姿态估计方法及系统.pdf
本发明公开了一种基于多尺度特征融合网络的二维手部姿态估计方法及系统。方法包括:收集原始手部单张彩色图像组成数据集并进行预处理;对训练集进行数据扩充处理;构建基于二维高分辨率热力图的多尺度特征融合网络,用于进行二维手部姿态估计;训练所述多尺度特征融合网络;以及将待估计手部单张彩色图像送入训练完成后的所述多尺度特征融合网络中获得预测的手部关节点的二维手部姿态。本发明方法采用二维高分辨率热力图提供了更准确且丰富的邻近区域手部关节点之间的相对位置信息,并将不同尺度的手部姿态特征加以融合,能够有效地提高对二维手部关