
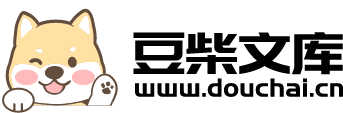
中频电炉炉衬的制作和节能减排的重要分析.pdf
yy****24
在线预览结束,喜欢就下载吧,查找使用更方便
相关资料
中频电炉炉衬的制作和节能减排的重要分析.pdf
中频电炉炉衬的制作和节能减排的重要分析中频电炉的炉衬使用次数,直接的制约着企业的生产效率,是节能减排的重要环节。中频电炉首先要选择优质的炉衬材料。熔化灰铁、球铁铁液一般选用二氧化硅为骨料配粘结剂硼酸等的酸性炉料。原则是,选用低导热系数、低膨胀系数、高稳定系数、高耐火度的优质炉衬材料,最好选取专业炉衬材料厂配制好的“捣打料”。炉衬材料生产国外厂家有联矿(天津)、拉法基乐法(上海)等,国内厂家有(湖北)华高,高能(武汉)等;需要什么种类和牌号的材料只需要提供给供应商所在单位熔炼合金种类、最高使用温度等参数即可
如何保护中频电炉的炉衬.ppt
如何保护中频电炉的炉衬?中频工业电炉的炉衬如何保护?1、炉容比:炉容比过大则会增加炼钢成本;炉容比过小则容易出现喷溅,降低炉衬使用寿命,不利于提高转炉生产率。因此在转炉生产过程中应保持设计时确定的炉容比。2、装入制度:确定转炉合理的装入量,合适的铁水、废钢比。在中频电炉www.jlgydl.com确定转炉装入量时,除了要考虑一个合适的炉容比外,还应保证适当的熔池深度,为保证炉底不受氧气射流的冲击,熔池深度必须超过氧流对熔池的最大穿透深度。3、供氧制度:确定科学、合理的供氧制度,保证杂质去除速度、熔池升温速
中频高温电炉炉衬烧结工艺.pdf
本发明公开了一种中频高温电炉炉衬烧结工艺,包括配制砂料、制造胚体、初期烘烤、铺石棉布、炉底打结、放置炉衬型芯、一次烧结、二次烧结、炉口打结九个步骤。本发明在选材上使用石英砂、铝镁尖晶石、耐火胶泥和硼酸,实现减少成本,降低环境危害。通过耐火胶泥的使用提高了炉衬的耐火度以及耐腐蚀度并有效防止炉漏,通过合理的粒度配比提升了炉衬的耐急冷急热性能,增加了炉衬的使用寿命,通过在感应器内侧铺石棉布以及反复的炉底打结制造出厚薄均匀、耐火度高的炉衬,并经过多次烧结,得到性能稳定的炉衬。
中频感应电炉炉衬捣打装置.pdf
本发明涉及一种中频感应电炉炉衬捣打装置,包括横跨在电炉上方的支架,在支架上设置有在支架上转动的螺杆,螺杆的下端固定连接有圆形的升降台,升降台呈水平布置,支架上设置有驱动螺杆转动以促使升降台实现上下运动的驱动机构;在升降台上至少设置有两个捣打器,捣打器包括设置于升降台上的伸缩油缸,伸缩油缸的伸缩端固定连接有弧形的捣打板,所述伸缩油缸通过基板设置于升降台上表面,基板上开设有腰形的调节孔,调节孔沿着升降台的直径方向布置,以及插入调节孔中且穿过升降台将基板与升降台形成锁定的锁紧件。本发明结构简单、使用方便,使得制
中频电炉打结复合炉衬新工艺.docx
中频电炉打结复合炉衬新工艺论文题目:中频电炉打结复合炉衬新工艺摘要:中频电炉是当代金属加工行业中常用的设备之一。然而,在使用过程中,由于高温与金属材料长时间接触,炉衬容易出现打结现象,从而导致设备性能下降、能源浪费等问题。为解决这一问题,本文提出了一种新的中频电炉打结复合炉衬工艺。通过结合使用不同材料的衬料,以及采用特定的复合工艺,可以有效地改善炉衬打结情况,确保设备的正常运行。本文将对该工艺的具体步骤、原理、优缺点进行阐述,并结合实例进行分析,为中频电炉打结问题的解决提供参考。关键词:中频电炉、炉衬、打