
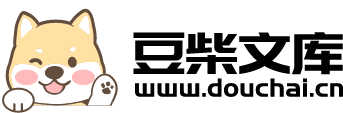
一种耐腐蚀铝合金及其制备方法.pdf
猫巷****盟主
在线预览结束,喜欢就下载吧,查找使用更方便
相关资料
一种耐腐蚀铝合金及其制备方法.pdf
本发明属于铝合金技术领域,本发明具体公开了一种耐腐蚀铝合金及其制备方法,所述的耐腐蚀铝合金由以下原料制备而成:镱、锆、镓、铈、铁、铬、镁、镍、锡、锌、余量铝。本发明通过以铝、锌、锡、镍为主要向合金原料,再添加镁、铬、铁、铈、镓、锆、镱,制备得到了性能稳定,强度高的铝合金,通过在本发明所述的性能稳定的铝合金以等离子熔覆法熔覆喷涂形成防腐蚀涂层能够显著提高所述铝合金的耐腐蚀效果,能够起到很好的保护作用,且所述的防腐蚀涂层表面均匀、致密性好,且所述的耐腐蚀涂层与铝合金本体具有良好的结合力。
一种耐腐蚀高强铝合金及其制备方法.pdf
本申请涉及新型航空铝合金材料领域,具体公开了一种耐腐蚀高强铝合金及其制备方法。一种耐腐蚀高强铝合金,由包含以下质量百分比的原料制成:镁0.55‑1.25%、铁0.08‑0.12%、铜1.3‑2.5%、锌0.15‑0.23%、铬0.07‑0.15%、钛0.05‑0.13%、镍0.03‑0.06%、硅0.32‑0.68%、锶0.06‑0.12%、锆0.05‑0.1%、改性石墨粉0.04‑0.06%、余量为铝;其制备方法为:先铝进行熔融,得到铝液,然后按比例加入其他组分原料进行熔炼,得到熔炼液;再向熔炼液中加入
一种耐腐蚀高温敏感铝合金及其制备方法.pdf
本发明公开了一种耐腐蚀高温敏感铝合金及其制备方法。本发明先对铝合金基体进行双面打磨,用碳酸钠、磷酸钠和十二烷基苯磺酸钠的混合液对铝合金基体进行表面处理,同时用超声波清洁,再用过氧化氢和十二烷基苯磺酸钠混合液对铝合金基体碱蚀,将硫酸镍、次磷酸钠、醋酸钠、苹果酸和乳酸制得的混合液对碱蚀处理的铝合金基体进行一次镀层,再用硬脂酸改性的氧化铈对一次镀层后的铝合金基体二次镀层,同时真空处理,最后对二次镀层的铝合金基体进行电化学形式的高温高压处理,制得耐腐蚀高温敏感铝合金。本发明制备的耐腐蚀高温敏感铝合金具有高强度、疏
一种耐腐蚀铝合金门窗及其制备方法.pdf
本发明公开了一种耐腐蚀铝合金门窗及其制备方法,该制备方法包括以下步骤:将铝、锡粉、镍粉等依次投入到反应炉中,依次经过扒渣,保温静置,铸造,均匀化退火,挤压成型,热处理,浸泡,喷涂,将铝合金表面清洗干净后,涂刷一层涂料,控制涂料漆膜干燥后的厚度为80‑100μm,在涂料,形成漆膜的表面继续涂刷另一层涂料;本发明所述的一种耐腐蚀铝合金门窗及其制备方法,通过熔化,扒渣,保温静置,铸造,均匀化退火,挤压成型,热处理,浸泡等工艺步骤能够显著提高铝合金门窗的防腐蚀性能以及铝合金韧性,可大大延长使用寿命,同时在铝合金门
一种高强度耐腐蚀的铝合金及其制备方法.pdf
本发明提供一种高强度耐腐蚀的铝合金及其制备方法,所述铝合金含有铝、硅、铁、镁、锰、铜、锌、钛、锡、铅、镍、铬组分,各组分的质量百分比为:硅10.8‑13.2%、铁0.6‑0.8%、镁≤0.1%、锰≤0.5%、铜0.8‑1.2%、锌≤0.55%、钛≤0.20%、锡≤0.10%、铅≤0.10%、镍≤0.3%、铬≤0.1%,余量为铝。所述铝合金的制备方法包括配料、投料熔化、合金化、成分调整、温度调整、除渣精炼、除气精炼、炉前检验、静置、浇铸、炉后检验、码锭包装、检斤入库等步骤。按照本发明的组分配比及制备方法生产