
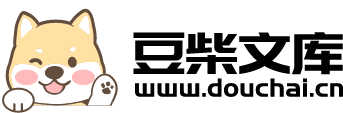
金属切削加工方法与设备.doc
kp****93
亲,该文档总共21页,到这已经超出免费预览范围,如果喜欢就直接下载吧~
相关资料
金属切削加工方法与设备.doc
金属切削加工方法与设备2.1金属切削机床的分类、型号及传动2.2车削加工2.3铣削、刨削和拉削2.4钻削与镗削加工2.5磨削加工2.6光整加工2.7齿轮齿形加工2.8特种加工技术概述车床下面首先通过几张图片使大家对金属切削机床与刀具有一个感性的认识。铣床磨床钻床铣削过程插齿过程滚齿过程拉齿过程1、机床的分类(1)按加工性质和加工刀具共分12类(表2.1)(2)按照机床通用性(万能程度)1)通用机床(万能机床):2)专门化机床(专能机床):3)专用机床:一、金属切削机床的分类、型号(3)按照加工精度:(4)
金属切削加工方法及设备.ppt
第三章金属切削加工方法及设备本节内容机床的组成金属切削机床的型号编制方法金属切削机床是一种用切削方法加工金属零件的工作机械机床—制造机器的机器,即工作母机或工具机,简称机床。机床工业在国民经济中占据重要地位,标志着一个国家的工业生产能力和科学技术水平。基本分类:2、机床的组成机床的组成(续)图2-35卧式车床的基本结构及运动1—主轴箱2—卡盘3—刀架4—后顶尖5—尾座6—床身7—光杠8—丝杠9—溜板箱10—底座11—进给箱图2-37立式钻床1—工作台2—主轴3—主轴箱4—立柱5—进给操纵机构图2-38摇臂
一种金属切削工具的加工方法及加工设备.pdf
本发明公开了一种金属切削工具的加工方法及加工设备,属于空气质量监测技术领域,包括以下步骤:获得毛坯,取尺寸大于所要加工切削刀具的毛坯,该毛坯一端具有能够夹持的延伸部,其中延伸部与毛坯位于同一长度方向;初步加工,加工毛坯使之接近所要加工切削刀具的形状,其中毛坯通过夹持延伸部以水平旋转的方式加工;成型加工,初步锻造的毛坯加工成型,并开设有利于排屑的槽口以及用于流体输送的孔洞。该金属切削工具的加工方法及加工设备,通过在所取毛坯上预留延伸部,并采用夹持延伸部以水平旋转加工成型的方式,使得毛坯受力均匀,既方便锻造加
第8章__金属切削加工方法与设备__教案.ppt
先进制造技术8.1电火花成型加工技术8.1.1电火花成型加工的基本原理8.2激光加工技术8.2.3激光加工2.激光加工的应用8.3超声波加工8.4高速与超高速切削技术1.高速主轴高速主轴单元是高速加工机床最关键的部件。目前高速主轴的转速范围为10000~25000r/min加工进给速度在10m/min以上。3.高性能的CNC控制系统CNC控制系统采用多个32位甚至64位CPU同时配置功能强大的计算处理软件使工件加工质量在高速切削时得到明显改善。相应地伺服系统则发
第3章 金属切削加工方法与设备 _教案.ppt
第三章3.1外圆表面的加工方法1.外圆表面的车削加工2.外圆表面的磨削加工3.外圆表面的精整、光整加工表3-1为外圆表面各种加工方案和经济加工精度3.2外圆表面车削加工表3-2车床的主要类型、工作方法和应用范围卧式车床的工艺范围很广如下图所示。如果再利用一些特殊附件那么卧式车床的工艺范围还能进一步扩大。2.CA6140卧式车床简介(3)CA6140卧式车床主要机构的调整图3-7前轴承间隙调整片式摩擦离合器间隙的调整制动器松紧的调整②溜板箱内主要机构的调整现象:加工时机动进给刀